Леонид Шевелев
Начальник инновационного отдела Департамента экономики металлургического комплекса Минэкономики России
За последние 10 лет (1987 1997 гг.) в мировой черной металлургии произошли серьезные структурные изменения. Металлургические комбинаты с полным циклом производства олицетворение эры индустриализации уходят в прошлое. На смену им пришли мини-заводы с электропечами и металлургическим сырьем, основанном на бескоксовой металлургии, с широким развитием технологии непрерывной разливки тонких слябов. Реструктуризация мировой черной металлургии характеризуется проникновением на рынок технологий жидкофазного восстановления железа углем, природным газом и другими дешевыми восстановителями вместо кокса. В электропечах используются заменители лома в виде металлизованных окатышей, горячепрессованных железорудных брикетов, синтикома, карбида железа...
Наибольший прорыв произошел в развитии мини-заводов, использующих электродуговые печи с установками разливки тонких слябов для производства полосовой стали. Первый крупный мини-завод с подобной технологической цепочкой был создан компанией «Ньюкор» (США) в 1989 году. В 1997 году производство полосовой стали мини-заводов такого типа составило 11,4 млн. т в США и 3,2 млн. т в странах Европы. Эти заводы все больше используют вместо лома первородное сырье (чугун, металлизованные окатыши, горячепрессованные брикеты, карбид железа, в последнее время синтиком и др.). Их продукция заполонила рынок высококачественных сталей, в частности, автомобильного листа, отличающегося низким содержанием цветных примесей: меди, никеля, хрома, молибдена, олова и др.
«Ромелт»: «всеядный», дешевый и экологичный
Итак, новое металлургическое сырье производится на основе прямого восстановления железа (ПВЖ). В 1997 году объем выпуска таких продуктов составил свыше 30 млн. т. Их производство на 90 % основано на использовании природного газа и железорудного сырья в виде крупнокусковой железной руды, агломерата и окисленных окатышей, в котором 65 % приходится на процесс «Мидрекс». Большая часть этого производства приходится на Латинскую Америку (36 %), затем следуют Ближний Восток (25 %) и Дальний Восток (24 %). Лишь 11,5 % мирового производства ПВЖ приходится на страны ЕЭК: Россия 5,4 %; Канада 3,3; США 1,5 %; Германия 1,3 %.
Среди других процессов ПВЖ, кроме «Мидрекса», получили развитие такие технологии, как «Корекс», «Карбид железа», «Ромелт», «Диос» и др., которые используются в промышленных масштабах или проходят испытания на демонстрационных установках.
Первая и единственная промышленная установка по производству карбида железа вступила в строй в Тринидаде в 1994 году. Она использует технологию переработки железорудной мелочи на основе природного газа. Номинальная производительность составляет около 300 тыс. т карбида железа в год.
«Корекс» представляет собой процесс восстановления железа углем и был разработан австрийской компанией «Фест-Альпине».
В технологии «Корекс» весь металлургический процесс идет в двух отдельных агрегатах: в шахтной печи с восстановительной атмосферой и в плавильном газогенераторе. Уголь и кислород подаются в плавильный газогенератор, что приводит к образованию восстановительного газа. После очистки от пыли этот газ подается в шахтную печь, где железорудная шихта восстанавливается в губчатое железо. Последнее с помощью шнековых конвейеров передается в газогенератор, где происходит процесс плавки. Процесс «Корекс» используется на фирмах: «Искор» (ЮАР), мощность 350 тыс. т в год, Поско (Южная Корея) 700 тыс. т в год, Джиндал (Индия) 1,5 млн. т, Ханбо (Южная Корея) 1,5 млн. т, Салданха (ЮАР) 650 тыс. т.
Процесс прямого восстановления железной руды «Диос» разработан в Японии и включает три печи с кипящим слоем. Жидкий чугун производится в печи жидкофазного восстановления, находящейся в основании системы «Диос». Вдувание кислорода осуществляется сверху, а снизу в эту печь подается азот. В настоящее время на предприятии компании «МКК» в Кейхине (Япония) работает опытная установка производительностью 150 тыс. т в год.
Технология «Ромелт» («русская плавка») разработана в России (Московский институт стали и сплавов). Восстановление и плавка осуществляются в одном агрегате. Восстановление железа происходит в пенистом шлаке. В качестве железорудного сырья могут использоваться: железорудная мелочь, железорудная пыль, шламы и другие низкокачественные сорта сырья. В качестве восстановителя используется дешевый энергетический уголь. Обогащенный кислородом воздух вдувается в шлак через фурмы, расположенные в нижней части агрегата, уменьшает плотность шлака и дает энергию для сжигания части угля. Чистый кислород вдувается через верхние фурмы и обеспечивает высокую степень последующего сжигания угля. Опытная установка производительностью 300 тыс. т в год смонтирована на Новолипецком металлургическом комбинате.
Ряд технологий прямого восстановления железа проходит опытное опробование с последующим вводом промышленных установок в 1998 2000 годах: «Хисмелт» (Австралия), «Аусмелт» (Австралия), процесс «циклонная печь-конвертер» (Нидерланды), «Фастмет» (Япония), «Финмет» (Австралия), «Сиркоред» и «Уиркофер» (Тринидад) и др.
Основным преимуществом новых технологий жидкофазного восстановления железа является использование дешевых некоксующихся углей и различных железосодержащих материалов. В частности, в жидкофазных процессах используется уголь с содержанием: связанного углерода 50 55 %; летучих 30 35 %; золы 12 15%. Для сравнения: в доменном производстве используется уголь с содержанием: связанного углерода 75 85 %; летучих 25 35 %; золы 8 10 %.
В качестве железорудного сырья в доменном процессе используются в основном дорогие подготовленные материалы: агломерат и окатыши. В процессах жидкофазного восстановления применяется в основном дешевая рудная мелочь, а также железосодержащая пыль, шлак и окалина («Ромелт»), за исключением «Мидрекса» и «Корекса», где используется крупнокусковая руда и окатыши. Это преимущество делает процесс «Ромелт» наиболее эффективным способом производства.
Важным преимуществом новых технологий является возможность корректировки их производительности для увязки с электродуговым производством в соответствии со спросом на рынке. В частности, новые установки могут работать в диапазоне 50 115 % их номинальной мощности, для остановки требуется 1 2 ч, а для запуска 3 5 ч. Доменные же печи работают только в строго постоянном режиме производительности, а их остановка является событием чрезвычайным и разорительным по последующим затратам.
Эксплуатационные издержки на производство чугуна в установках жидкофазного восстановления примерно в 2 раза ниже по сравнению с доменным производством и составляют: в доменном производстве 64 долл./т чугуна, в процессах жидкофазного восстановления 24 38 долл./т чугуна, в том числе «Ромелт» 29 долл./т, «Корекс» 35 долл./т.
Еще более высоким преимуществом обладают новые технологии по сравнению с доменным производством в плане охраны окружающей среды. В частности, объемы выброса пыли и содержания вредных элементов в процессе жидкофазного восстановления в 4 раза ниже по сравнению с доменным производством.
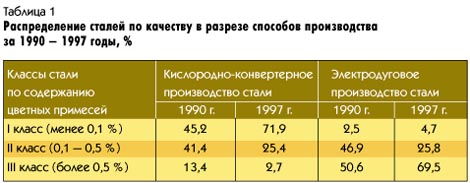
«Классическая» металлургия под натиском инноваций
Велики перемены в технологии электросталеплавильного производства. Такие инновационные решения, как использование дуги постоянного тока, предварительный нагрев лома, вдувание кислорода, применение новых железосодержащих материалов вместо лома и др., способствовали резкому повышению производительности, сокращению электропотребления, снижению себестоимости стали.
В электросталеплавильном производстве большое внимание при использовании железосодержащих материалов уделяется содержанию в них примесей цветных металлов: меди, никеля, хрома, молибдена и олова. Эти элементы значительно ухудшают качество стали по прочности, пластичности, вязкости, что в конечном итоге приводит к поверхностным дефектам готовых изделий проката, труб, метизов... В новых материалах, полученных на основе процессов жидкофазного восстановления, суммарное содержание этих примесей не превышает 0,01 %, т. е. в 30 раз меньше, чем в ломе, и приближается к содержанию их на уровне чугуна, полученного доменным способом из первородного сырья. Применение новых материалов при производстве стали электродуговым способом вместо лома позволяет получить почти такие же показатели по чистоте содержания вредных цветных примесей, как и при производстве стали кислородно-конвертерным способом с использованием чугуна.
Как видно из приведенных данных, интегрированные металлургические предприятия, использующие технологию кислородно-конвертерного производства стали с применением чугуна, наиболее приспособлены для производства слябов с получением высококачественной листовой стали для глубокой вытяжки, с высокой прочностью, пластичностью и вязкостью, хорошим уровнем поверхности (автолист, трубы, прокат с покрытием для бытовых изделий и приборов и др.). При производстве стали электродуговым способом их доля в данном классе качества составляет небольшую величину, но она также возросла почти в 2 раза.
Во II классе качества производятся в основном блюмы и заготовки с получением катанки и сортовых профилей. Их доля и тенденции изменения в обоих способах производства сталей (кислородно-конвертерном и электродуговом) одинаковые, т. е. имеет место снижение их уровня. При этом в кислородно-конвертерном способе это уменьшение произошло в сторону увеличения I класса качества, а в электродуговом способе в сторону III класса качества, в основном в сторону увеличения легированных марок стали. Оба способа производства четко отслеживают на рынке свой сектор: кислородно-конвертерный высококачественная углеродистая сталь; электродуговой легированная сталь. Тем не менее применение новых материалов в электродуговом способе производства, полученных жидкофазным восстановлением с низким содержанием вредных цветных примесей, позволяет потеснить на рынке стали кислородно-конвертерную сталь в I классе качества, в частности, в производстве полосовой стали. Поэтому замена мартеновских печей электропечами нового поколения с комплексом установок жидкофазного восстановления, внепечной обработкой и непрерывной разливкой в тонкие слябы имеет актуальное значение в реструктуризации черной металлургии России, в повышении ее конкурентной способности на мировом рынке стали в XXI веке.
2000 год: «фифти-фифти»...
По оценке международных экспертов ЕЭК ООН, выплавка стали по видам продукции и способам производства к XXI веку изменится следующим образом (см. табл. 2).
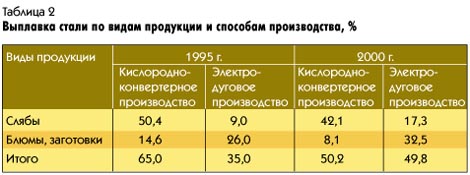
Как видно из приведенных данных, производство стали в электропечах к 2000 году возрастет более чем на 40 % и достигнет равного, как говорят «фифти-фифти», уровня с кислородно-конвертерным способом производства.
Кислородно-конвертерный способ на интегрированных заводах будет по-прежнему ориентирован на выпуск высококачественного листового проката. Однако при этом на рынке стали доля листового проката, производимого на мини-заводах с электродуговым способом производства, возрастет с 9 до 17,3 %, т. е. увеличится почти в 2 раза.
Такой рост возможен как при существенном увеличении производства заменителей лома в виде новых материалов жидкофазного восстановления, так и благодаря модернизации самих электропечей, обеспечивающих резкое снижение электропотребления и уменьшение на этой основе себестоимости стали.
Увеличение производства и потребления заменителей лома будет продолжаться при условии снижения цен на них по сравнению с ценами на лом, или если при их использовании снизится себестоимость стали. По оценке международных экспертов ЕЭК ООН, при мировом производстве стали на уровне 750 800 млн. т в год (в 1997 г. 785 млн. т) цены на лом составят 120 140 долл./т. При этом цены на заменители лома составляют 125 145 долл./т с уровнем рентабельности 12 % с учетом транспортных расходов. Цены на жидкий чугун составят 140 150 долл./т. Заменители лома обеспечат определенный экономический эффект в сталеплавильном производстве за счет повышения выхода годного, снижения энергопотребления, повышения производительности. Это наглядно видно на примере использования синтикома (табл. 3). Эффективность технологии производства новых материалов процессами жидкофазного восстановления приведена на примере «Ромелта» (табл. 4).
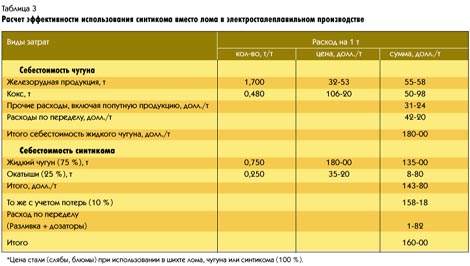
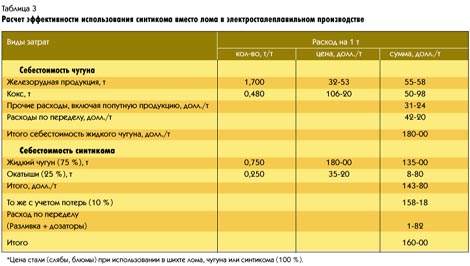 Запад страсть как экономит...
Применение новых технологий в области электродугового производства стали (ЭДП) способствовало сокращению издержек производства и получению таких марок стали, которые прежде производились лишь в кислородных конвертерах.
Совершенствование технологий ЭДП определяется по расходу электроэнергии и электродов на тонну жидкой стали, к их числу относятся: предварительный нагрев лома, применение ковшовой металлургии, повышение мощности трансформаторов и использование постоянного тока. Добавим к этому перечню вдувание кислорода и впрыскивание угольно-кислородной смеси, применение распылительных горелок, выпуск плавки через эксцентрический под и др. Учитывая разный характер использования новых технологий в электродуговом производстве стали в Западной и Восточной Европе, изменение основных показателей приведено в разрезе регионов (см. табл. 5).
Как видно из приведенных данных, в этих регионах за рассматриваемый период (1990 1997 гг.) произошло значительное снижение расхода электроэнергии, электродов и затрат труда, улучшился выход годной стали, возросла производительность электропечей.
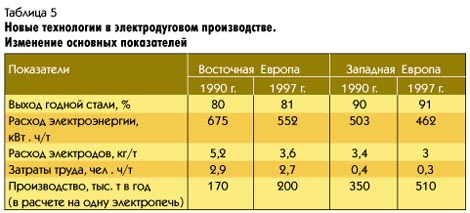
Вместе с тем, объем внедрения новых технологий в Западной Европе значительно больше, чем в Восточной Европе, что и привело к различиям в расходе электроэнергии, электродов и затрат труда. В частности, в электродуговом производстве в Западной Европе по сравнению с Восточной Европой расход электроэнергии ниже на 35,4 %, расход электродов на 20 %, затраты труда в 9 раз, а производительность печей выше почти в 2 раза. В настоящее время новые конструкции электродуговых печей в странах ЕС обеспечивают расход электроэнергии менее 350 кВт . ч/т и расход электродов до 1,6 кг/т. При цене электроэнергии 0,06 долл./т, электродов 2,5 долл./кг переход на новые конструкции печей обеспечит снижение издержек производства в странах Восточной Европы на 23,6 долл./т стали, в странах Западной Европы на 11,9 долл./т стали. Использование новых конструкций электродуговых печей позволяет получать в них сталь в виде блюмов и заготовки (II класс качества с применением лома) по себестоимости ниже кислородно-конвертерной стали аналогичного класса качества на 4,9 долл./т стали.
С учетом меньших амортизационных затрат за счет применения бескоксовой металлургии себестоимость стали в электродуговых печах по I классу качества (полосовой прокат для автолиста) на мини-заводах получается ниже, чем на интегрированных заводах на 12 15 % (без учета непрерывной разливки в тонкослябовых установках), что и обеспечивает ее конкурентоспособность в аналогичном секторе рынка высококачественной углеродистой стали.
Где тоньше, там и дешевле
Толщина слябов, получаемых при применении технологии разливки тонких слябов, колеблется в пределах 40 125 мм, в то время как на обычных установках 150 350 мм. Кроме того, тонкослябовые установки действуют в едином технологическом комплексе со станами горячей прокатки, что позволяет снизить объем энергопотребления. На новых тонкослябовых установках имеется возможность получения горячекатаной полосы толщиной менее 1 мм. Такие результаты уже получены на заводе «Ньюкор Хикмэнарк» (0,44 мм). Это свидетельствует о том, что интегрированные предприятия полного цикла могут оказаться неконкурентоспособными, если мини-заводам электродугового производства стали удастся решить проблему качества поверхности тонкого листа, обеспечивающего производство сортов стали для глубокой вытяжки. Последние, в частности, идут на изготовление внешних частей автомобилей. Пока качество поверхности тонких слябов получается ниже, чем на обычных установках непрерывной разливки стали, в основном за счет более низкой температуры при входе сляба в стан горячей прокатки: на тонких слябах без подогрева 1100 1150оС, на толстых слябах (из печи) 1250оС. При этом достигается снижение удельного энергопотребления с 1100 мДж/т (на толстых слябах) до 460 мДж/т (на тонких слябах). Затраты труда на тонкослябовых установках составляют 0,37 чел . ч/т, а на толстых 0,59 чел . ч/т. Денежные издержки на тонкослябовых установках составляют 28,8 долл./т, а на толстых слябах 35,5 долл./т (эксплуатационные расходы). С учетом всех издержек производства (энергозатрат, трудовых затрат и финансовых расходов) себестоимость стали на тонкослябовых установках получается на 17 20 долл./т ниже, чем на обычных.
Элитные сорта стали последнее прибежище стальных гигантов
В последние годы наметилась новая тенденция в общем объеме мирового производства стали. Происходит рост доли мини-заводов с электродуговым производством. Рост имеет устойчивый характер и сохранится в будущем. Новые технологии производства заменителей лома на базе жидкофазного восстановления, совершенствование технологий электродугового производства стали в сочетании с совершенствованием конструкции электропечей, переход на тонкослябовые установки все это в совокупности обеспечивает мини-заводам с ЭДП выход на рынки, которыми раньше владели интегрированные предприятия с кислородно-конвертерным способом производства стали.
Повышение качества стали на мини-заводах, использующих электродуговое производство стали, является наиболее актуальной проблемой повышения их конкурентоспособности. Производители электростали вынуждены непосредственно заняться производством заменителей лома на базе технологий жидкофазного восстановления, включая и создание совместных предприятий. Расширение сферы использования новых технологий будет играть ключевую роль в процессе принятия инвестиционных решений. Учитывая низкие капитальные затраты на установки жидкофазного восстановления железа по сравнению с доменными печами, коксовыми батареями и аглофабриками, можно полагать, что для создания новых сталеплавильных мощностей будут, главным образом, использоваться эти технологии. В ближайшем будущем действующие предприятия, использующие классическую технологию доменного производства, будут в большинстве своем переоснащаться, а не заменяться этими новыми технологиями. Совершенствование электродугового комплекса в технологической цепочке электропечь заменители лома тонкослябовые установки позволит получить качество стали, аналогичное с кислородно-конвертерным способом производства, снизить текущие и капитальные издержки производства. Дело идет к тому, что мини-заводы поставят под угрозу рентабельность производства продукции на интегрированных предприятиях полного металлургического цикла. Интегрированные предприятия с полным циклом и обычными установками непрерывной разливки стали, чтобы выжить, должны ориентироваться главным образом на рынок высококачественной продукции и стремиться к повышению добавленной стоимости в составе своей продукции за счет реализации стратегий интеграции производства «вверх по производственно-технологической цепочке».
|