Юрий Адно
Пожалуй, одним из наиболее ярких моментов в послевоенном развитии мировой черной металлургии стал быстрый рост числа и стремительное повышение роли так называемых мини-заводов передельных предприятий сравнительно небольшой мощности (в среднем около 500 тыс. т стали в год). Сегодня эти предприятия представляют весьма перспективное направление металлургического производства, основу которого на протяжении десятилетий традиционно составляли крупные производственные комплексы с полным металлургическим циклом (интегрированные заводы, комбинаты), включающие, как правило, все основные переделы. Динамичное развитие мини-заводов в составе отрасли, главным признаком которой обычно являлся высокий уровень концентрации и монополизации производства, отражает, на наш взгляд, своеобразие и сложность процесса ее структурной перестройки.
Уязвимость и опасную инерционность металлургических гигантов этих индустриальных Левиафанов, пожирающих горы сырья и моря энергии, выявили в периоды острых кризисов 1974 1975 гг., и особенно 1980 1982 годов. Напротив, высокую рентабельность и жизнеспособность продемонстрировали удачливые "внуки Левиафана" мини-заводы, которые гибко приладились к изменениям рынка в кризисные периоды. Тогда из-за глубокого спада западные сталелитейные корпорации понесли огромные убытки, а мощности не были загружены.
Мини-заводы получили развитие как одно из ведущих направлений рационализации производства в черной металлургии. Более того, по мнению некоторых экспертов, современные мини-заводы представляют особую самостоятельную разновидность черной металлургии с вполне сформировавшейся технологической, организационной, сырьевой и продуктовой спецификой.
Вверх по лестнице, ведущей вниз
Небольшие металлургические заводы существовали всегда. Нередко они были придатками крупных компаний и выполняли вспомогательные функции по изготовлению отдельных видов полуфабрикатов или готовой продукции. Зачастую эти заводы имели сравнительно отсталую технологию и достигали приемлемого уровня рентабельности главным образом за счет высокой степени эксплуатации персонала. К категории мини-заводов относятся, как правило, предприятия, имеющие высокоэффективную технологическую схему и организационную структуру, а также продуктовую специализацию для удовлетворения потребностей определенного рынка.
За последние 20 лет сформировались новые экономические условия, предопределившие появление в черной металлургии небольших предприятий нового типа, а также характер их сосуществования с крупными заводами. Здесь в первую очередь следует назвать чрезвычайно высокий, по-видимому, близкий к предельному, уровень концентрации производства в черной металлургии. На протяжении многих десятилетий развитие отрасли шло по линии последовательного укрупнения агрегатов и предприятий. Оба процесса протекали параллельно, как бы дополняя друг друга. К середине 70-х годов в мировом производстве и на рынке металлопродукции ведущую роль играли компании, имеющие заводы с годовой мощностью не менее 5 млн. т стали. В одной Японии работали 10 таких предприятий. Оборудование этих гигантов составляли доменные печи объемом до 4 5 тыс. м3, кислородные конвертеры емкостью 300 350 т, прокатные линии с годовым производством 6 7 млн. т широкой стальной полосы. Основа индустриальной мощи страны черная металлургия неизменно ассоциировалась с лесом труб, огромными корпусами цехов и доменных печей, облаками дыма, пыли и удушливых газов. Производственный процесс на таких заводах связан с колоссальными затратами сырья, энергии, вспомогательных материалов, строительством мощных очистных сооружений. Индустриальный Левиафан стал угрозой для окружающей среды целых стран. К тому же существование металлургических гигантов требует организации дорогостоящих и весьма объемных транспортных перевозок, в том числе трансконтинентальных. К слову сказать, при переходе к рыночным отношениям транспортная составляющая в металлургии России достигла 16 % от себестоимости и подрывает эффективность экспорта. В условиях нестабильного спроса на металлопродукцию при неравномерном циклическом развитии экономики обеспечивать устойчивую и, следовательно, экономически эффективную и рентабельную работу таких громоздких предприятий чрезвычайно сложно. Бесконечное наращивание единичной мощности металлургических производств в плане рыночной конкурентоспособности оказалось движением вверх по лестнице, ведущей вниз.
В то же время в начале 90-х годов в мире функционировали (и весьма успешно!) около 390 мини-заводов общей годовой мощностью более 200 млн. т стали, что составляет около 20 22 % мировой мощности. Только в США сегодня действуют (а также находятся в стадии строительства и монтажа) около 60 предприятий подобного типа общей мощностью около 25 млн. т стали в год (примерно четверть сталеплавильного потенциала страны).
Каковы же причины, обусловившие появление и быстрый рост мини-заводов в составе черной металлургии?
Это, во-первых, низкие удельные капиталовложения и короткий строительный цикл, сравнительно простая и компактная технология, относительно доступное сырье в виде металлического скрапа, специализированный сортамент продукции, ориентированный на конкретного потребителя, и, во-вторых, высокая производительность труда и низкий уровень производственных издержек.
Сооружение мощных заводов полного цикла требует больших инвестиций и затягивается на долгие годы. В США, например, удельные капвложения в создание интегрированного завода сегодня превышают, по некоторым оценкам, 2 тыс. долл. на тонну мощности, что примерно в 6 8 раз превосходит уровень конца 60-х годов. Постоянный рост капиталоемкости металлургического производства в последние десятилетия не компенсируется соответствующим наращиванием производительности основных агрегатов, так как растущая доля капитальных затрат расходуется на повышение экологической безопасности, развитие систем управления, маркетинга и т. д. Только затраты на экологию возросли в общем объеме капвложений с 3 5 % в 60-е годы до 20 25 %, достигнув уровня инвестиций в основные металлургические переделы.
Сравнительно низкая коммерческая прибыльность, обусловленная несбалансированностью между растущими издержками и сравнительно стабильными ценами на металлопродукцию на рынке, существенно ограничивает возможности привлечения капитала для модернизации производства и диктует выбор наиболее экономичного пути развития.
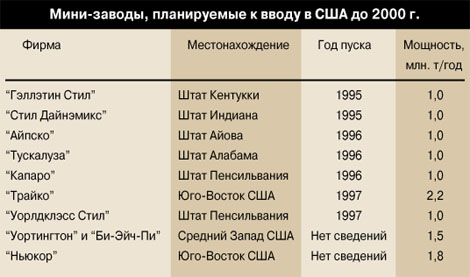
Везде, даже на Гавайях
Технологическую концепцию мини-завода отличают компактность, простота, надежность. Техническую основу составляют два основных передела: сталеплавильный (электродуговая плавка) и прокатный (непрерывная прокатная линия), органически связанные машиной непрерывного литья заготовок.
Некоторые проблемы могут быть связаны с сырьем, в качестве которого обычно используется металлический лом (амортизационный и оборотный). Ресурсы этого сырья в целом достаточны, однако в нем растет доля амортизационного лома (промышленные и бытовые отходы, скрапированное оборудование, списанные автомобили и др.), загрязненного вредными примесями, что требует предварительной очистки и сортировки. Альтернативным сырьем служат также продукты прямого восстановления железной руды металлизованные окатыши.
Типичный мини-завод мощностью 0,5 1 млн. т стали в год обычно включает 1 2 электродуговые печи емкостью 70 130 т, 1 2 машины непрерывного литья стальных заготовок (МНЛЗ), непрерывный мелкосортно-проволочный стан. Узкоспециализированный марочный и профильный сортамент продукции чаще всего составляют простой сортовой профиль, катанка, строительная арматура (в последние годы полоса). Такая технологическая схема обеспечивает высокую эффективность производства и низкие отходы, исключает использование дорогостоящего сложного оборудования (аглофабрик, коксовых батарей, доменных печей, блюмингов и слябингов).
В первую очередь следует отметить низкие удельные капитальные затраты мини-заводов по сравнению с предприятиями традиционного типа. Это достигается благодаря отсутствию дорогостоящих и наиболее грязных рудоподготовительного и коксодоменного переделов, а также вытекающим отсюда низким затратам на охрану окружающей среды и развитие заводской инфраструктуры. Большую экономию дает использование высокопроизводительного типового оборудования. Средние удельные инвестиции в сооружение современного мини-завода различной модификации в 3 5 раз ниже, чем для комплексов полного цикла. Кроме того, они довольно быстро возмещаются из-за малой продолжительности строительного цикла. Как правило, проектирование и сооружение этих предприятий ведутся одновременно и весь процесс длится не более 12 20 месяцев, поскольку оборудование обычно монтируется из типовых стандартных элементов. Большинство мини-заводов чаще всего ориентированы на местный региональный рынок отсюда низкий уровень транспортных расходов. В США, например, до недавнего времени оптимальным считалось расстояние от завода до основных потребителей в пределах 500 миль. Большинство американских мини-заводов расположено в районах, где нет или почти нет предприятий классического типа, например в штатах Техас и Калифорния и даже в курортных Флориде и Гавайях.
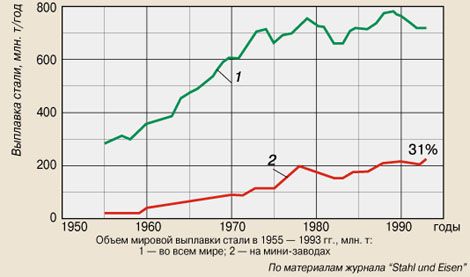
Металлолом как кладезь энергии
Для мини-заводов характерна низкая энергоемкость производства. При использовании металлолома экономия энергии составляет около 70 % по сравнению с выплавкой стали из первичного рудного сырья по традиционному технологическому маршруту: доменная печь кислородный конвертер. Сторонники мини-заводов иногда даже называют стальной скрап "носителем энергии", имея в виду, что он как бы аккумулирует значительную часть энергии, необходимую для первичных стадий металлургического цикла.
Мини-заводы обеспечивают самый низкий в черной металлургии уровень затрат живого труда и высокую производительность. Это вытекает как бы само собой из-за использования автоматизированного оборудования, работающего в непрерывном режиме, высокой специализации сортамента, простой и гибкой технологической и организационной структуры производства и управления. На современных мини-заводах США производство 1 т металлопродукции в среднем требует около 1 человеко-часа, что примерно втрое ниже, чем на самых передовых заводах полного цикла. Наиболее современные заводы компании "Ньюкор" сумели даже снизить этот показатель еще в 2 2,5 раза.
К очевидным преимуществам мини-заводов можно отнести также пониженную степень риска при внедрении технологических новинок. Многие достижения последних десятилетий были впервые опробованы в промышленном масштабе на мини-заводах. В их числе процессы прямого восстановления руды, конвертер с комбинированной продувкой, непрерывные процессы выплавки стали, различные модификации литейно-прокатных агрегатов.
Все это обеспечивает высокую экономическую эффективность мини-заводов, играющих активную роль на рынке определенных видов металлопродукции. Например, в конце 80-х годов мини-заводы США производили почти всю арматурную сталь, 85 % легких сортовых профилей, более 80 % катанки, около 40 % специальных видов сортового проката.
Разумеется, мини-заводы при всей их экономической привлекательности не смогли решить все сложные проблемы развития черной металлургии. Главная причина ограниченный и довольно однообразный сортамент металлопродукции (до последнего времени главным образом сортовой прокат и катанка). А это уже не отвечает растущим потребностям современной рыночной экономики.
"Ньюкор" и "Шлеман-Зимаг" лидеры рынка
До недавнего времени практически неразрешимой представлялась проблема: как рационально технологически сочетать экономические преимущества узкоспециализированного производства мини-завода с рентабельным промышленным выпуском более широкого сортамента металлопродукции, в первую очередь листового проката, в соответствии с требованиями рынка. В этой связи поистине революционным достижением технологии стали разработка в конце 80-х годов фирмой "Шлеман-Зимаг" (ФРГ) и промышленное внедрение в США (а затем и в других странах) способа непрерывного литья тонких слябов технология CSP (Compact Strip Production). Процесс CSP и появившиеся в последние годы его модификации позволяют разливать на машинах непрерывного литья тонкие слябы, близкие по размерам к готовой продукции, и напрямую прокатывать их на готовую полосу толщиной 1,8 2 мм и шириной до 1,5 м за один нагрев. Достоинства способа: компактность, сравнительная простота обслуживания, высокая технологическая гибкость, снижение капитальных затрат почти на 35 % и производственных почти на 20 % по сравнению с традиционной технологией при хорошем качестве продукции. Это определило весьма динамичное развитие процесса CSP. Первые промышленные установки подобного типа появились в США на одном из мини-заводов компании "Ньюкор" в 1989 г. Сегодня компания является мировым лидером по развитию этой технологии. Общая годовая мощность заводов компании составляет около 4 млн. т стали и в ближайшие годы, по-видимому, возрастет до 10 млн. т. Это означает, что компания, владеющая исключительно мини-заводами, займет одно из ведущих мест среди главных сталеплавильных корпораций США, имеющих заводы полного цикла.
Мини-заводы переживают бум
Нынешний подъем и весьма динамичная структурная перестройка черной металлургии США в значительной степени связаны с развитием этого направления мини-металлургии. Облик старейшей отрасли все больше приближается к структуре так называемой "постиндустриальной" экономики. К началу нового столетия, т. е. в ближайшие 5 лет, предполагается ввести в строй не менее 10 мини-заводов общей годовой мощностью около 13 млн. т стальной полосы различного вида, в том числе с антикоррозионным покрытием, что еще больше расширит рыночные возможности и повысит авторитет этого сектора черной металлургии. По прогнозам, доля мини-заводов может составить более 10 % общего выпуска полосового проката в стране. При этом продолжатся строительство и модернизация "традиционных" мини-заводов первого поколения, выпускающих сравнительно простой сортовой металл и катанку. Довольно реальными представляются оценки производства мини-заводов до 40 % всей стали в стране в начале будущего десятилетия.
Очевидные рыночные преимущества мини-заводов стимулировали их строительство в различных регионах мира, в том числе в развивающихся странах (Индия, Мексика, Тайвань, Сингапур, Индонезия, Тайланд и др.).
Технический прогресс способствовал оптимизации размеров мини-заводов. Например, сегодня для производства полосового проката экономически выгоден годовой объем выпуска не менее 1 млн. т. Уже появились предприятия этого типа с годовой мощностью 2 млн. т и более.
Быстрый рост мини-металлургии повысил спрос на стальной лом, что вызвало его удорожание в большинстве развитых стран. Это, в свою очередь, активизировало поиск новых более экономичных и экологичных промышленных способов производства передельного чугуна, губчатого железа и другого сырья для выплавки стали.
Однако, по нашему мнению, совершенно нереально представить будущую черную металлургию, состоящую исключительно из одних мини-заводов. Для нормального развития любой экономической системы характерна органическая связь концентрации и специализации производства, что обуславливает многоразмерность предприятий внутри любой отрасли. С учетом отраслевой специфики в черной металлургии скорее всего будут оптимально сочетаться, взаимно дополняя друг друга, предприятия различной специализации и размера. Весьма вероятно, что по мере дальнейшего развития научно-технического прогресса границы между интегрированными и мини-заводами будут нивелироваться. Уже сегодня, например, реализуются проекты интегрированных мини-заводов, имеющих компактный и экономичный передел по производству сырья для выплавки стали. В свою очередь, мини-заводы будут, по-видимому, эволюционировать в направлении расширения сортамента и видов применяемых шихтовых материалов. Количественные пропорции развития этих процессов будут определяться особенностями развития экономики конкретной страны.
Эти структурные изменения в целом будут способствовать повышению эффективности производства и укреплению позиций черной металлургии в структуре будущего "технотронной" экономики XXI века.
|