Вячеслав Кротков Генеральный директор ОАО "Атомредметзолото", академик Российской академии горных наук и Международной академии минеральных ресурсов
Происшедшие за последнее десятилетие изменения в социальном строе страны, распад Советского Союза привели к тому, что в пределах Российской Федерации осталось лишь одно из девяти уранодобывающих предприятий, ранее объединенных в структуре Минсредмаша. Вместе с тем Россия заинтересована не только в надежном сырьевом обеспечении собственной атомной промышленности, но и в сохранении своих позиций в мировом рынке. Это обстоятельство, а также изменившаяся конъюнктура рынков уранового минерального сырья потребовали поиска более прогрессивных и более дешевых технологий производства природного урана.
В этих условиях особый интерес представляют нетрадиционные технологии, разработанные в научных подразделениях и освоенные на предприятиях отрасли.
По мере развития добычи урановых руд определенное количество урана остается в недрах, в так называемых некондиционных рудах, в зонах обрушения, целиках и т.д., отработка которых традиционным горным способом является экономически нерентабельной. В результате эти руды практически навсегда утрачивались.
Силами отраслевых институтов Всесоюзного научно-исследовательского института химической технологии (ВНИИХТ), Всесоюзного проектного и научно-исследовательского института промышленной технологии (ВНИПИпромтехнологии) Первого Главного горного управления Минсредмаша (ныне ОАО "Атомредметзолото"), ряда сторонних научных организаций совместно с научно-исследовательскими организациями и производственниками предприятий отрасли в 1961 году были начаты работы по созданию новых нетрадиционных технологий добычи урана из недр. Опираясь на успехи физики, химии, гидрогеологии и других наук в части возможности изменения хода естественных геохимических и гидрогеологических процессов в недрах земли и возможности высокой степени извлечения урана из водных растворов с помощью ионообменных смол, была обоснована рентабельная добыча урана и других металлов путем химического растворения их соединений из руд без извлечения последних из недр, а также выщелачиванием в штабелях (кучах) из попутно добытых традиционным способом низкосортных и некондиционных руд.
Лермонтовское горно-химическое рудоуправление (ЛГХР) явилось пионером внедрения этой технологии на месторождении Бык при отработке урановых руд на месте их залегания.
После извлечения балансовых руд встал вопрос о закрытии рудника 2, отрабатывавшим это месторождение, хотя оставались большие запасы забалансовых руд. Чтобы эффективно использовать этот ресурс, было решено применить нетрадиционную горно-химическую технологию. Перед инженерно-техническими работниками предприятия и научно-исследовательскими организациями встала сложная задача: в течение короткого срока внедрить в промышленном масштабе новый способ добычи урана.
После успешно проведенных опытных работ началась отработка забалансовых руд Быкогорского месторождения способом подземного выщелачивания (ПВ), которая быстро достигла промышленных масштабов. Несмотря на низкое содержание урана в рудах (0,014 0,020 %), полученные технико-экономические показатели оказались более высокими, чем при добыче традиционным горным способом балансовых руд, где содержание урана было в четыре и более раз выше.
Подготовка блока для выщелачивания урана заключалась в этажной (подэтажной) отбойке руды глубокими скважинами в зажатой среде с последующим ее магазинированием в камере. Затем руда орошалась инфильтрационным потоком водного раствора серной кислоты для перевода урана в раствор. Обогащенные ураном растворы собирались в растворосборник и откачивались на поверхность для получения готовой продукции (закиси-окиси урана) на гидрометаллургическом заводе.
Коэффициент разрыхления рудной массы в блоке после взрыва составлял 1,15 1,20.
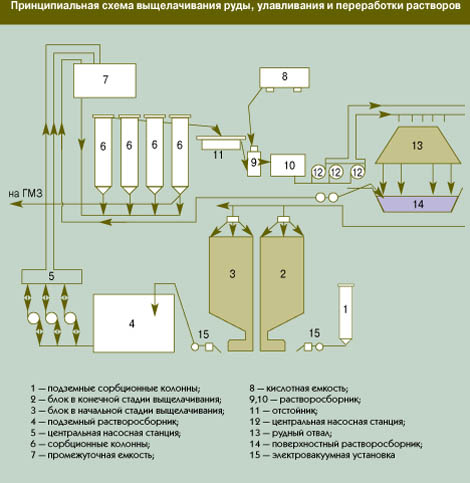
В результате совершенствования схем подготовки блоков были значительно сокращены объемы подготовительных и особенно нарезных работ. Доля мелкошпуровой отбойки горнорудной массы в общих объемах сократилась с 7,8 % до 2,2 %, а себестоимость отбойки 1 м3 снизилась на 20 %. Производительность труда рабочих горного цеха выросла в 2,2 раза. Содержание пыли в рудничной атмосфере снизилось на 30 %, влияние продуктов распада радона на организм занятых здесь людей на 20 %. Кроме того, последовательные усовершенствования подготовки блоков к выщелачиванию позволили ликвидировать оставление межблоковых целиков и перейти к бесцеликовой отработке рудных тел.
В дальнейшем по отдельным рудным телам и залежам, где горно-геологические условия позволяли выщелачивать уран из рудного массива без его дробления, была внедрена схема подготовки блоков для выщелачивания урана без нарушения естественной структуры массива. Данной технологией в последние годы работы рудника 2 добывалось до 25 30 % урана от общего объема.
Пробные выпуски выщелоченной руды из блоков показали, что содержание урана в них колеблется в очень незначительных пределах. Среднее содержание составляло 0,007 % и, как правило, мало зависело от изменения содержания урана в замагазинированной руде. Отсюда был сделан вывод, что процент извлечения урана при выщелачивании находится в прямой зависимости от его содержания в замагазинированной руде.
В практической деятельности помимо этого фактора на извлечение урана и, как следствие, его себестоимость в продуктивном растворе в значительной степени влияют: вещественный состав и входящие в него минеральные ассоциации руд и вмещающих пород, наличие тектонических экранов, эффективная пористость, коллекторские свойства пород и ряд других физико-химических и физико-механических свойств горнорудного массива.
Внедрение горно-химической технологии добычи урана на руднике 2 ЛГХР показало ее достаточно высокую эффективность. При снижении содержания урана в отрабатываемых рудах более чем в четыре раза по сравнению с балансовыми рудами, отработанными ранее по традиционной горной технологии, себестоимость готовой продукции (уран в закиси-окиси) удалось не только сохранить на прежнем уровне, но даже снизить на 18 %. Кроме того, в отработку дополнительно были вовлечены забалансовые запасы руды, в три раза превышающие по количеству урана подсчетные балансовые запасы.
Практикой применения данного способа добычи урана на руднике 2 доказано, что забалансовые руды являются дополнительным источником увеличения сырьевой базы уранодобывающей подотрасли.
Как показала 40-летняя практика добычи урана на руднике 2 и других предприятиях отрасли, нетрадиционной технологией в процесс выщелачивания вовлекаются уран и другие металлы, находящиеся не только в забалансовых рудах, но и во вмещающих породах с повышенным кларковым содержанием. Из всего сказанного можно сделать вывод, что при добыче урана горно-химической технологией из плотных, так называемых "скальных", руд становится экономически целесообразным отрабатывать бедные и забалансовые руды, а также вовлекать в отработку труднодоступные по техническим условиям рудные тела, которые экономически нецелесообразно отрабатывать традиционным горным способом.
Снижение себестоимости конечной продукции при горно-химической технологии более чем в два раза является следствием исключения и сокращения ряда дорогостоящих и трудоемких технологических процессов и переделов, неизбежных при традиционном горном способе добычи и переработки руды, таких, как:
подземная транспортировка и выдача до 85 % руды из-под земли на поверхность и доставка ее от рудника до гидрометаллургического завода (ГМЗ);
дробление и измельчение руды на заводе;
транспортировка и складирование хвостов гидрометаллургического передела.
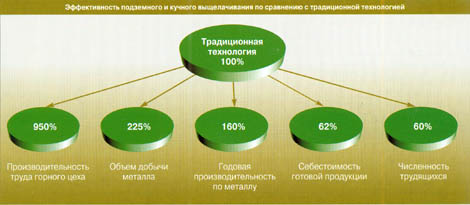
Помимо экономических преимуществ, внедрение горно-химической технологии на рудниках способствовало резкому снижению травматизма на горных работах за счет сокращения объемов особо опасных, тяжелых и вредных условий труда горняков, автоматизации производственных процессов, достижению высокой производительности труда. В объемных показателях производительность труда подземных горнорабочих выросла в 8 10 раз, а рабочих горного цеха по выпуску готовой продукции в 1,5 2 раза.
Важным достоинством новой технологии явилось и то, что руда после выщелачивания оставляется в недрах, на месте залегания. Этим исключается ее вредное влияние на воздушный и водный бассейны.
Результаты научно-исследовательской деятельности и практический опыт отработки Быкогорского месторождения горно-химической технологией добычи урана из "скальных" руд были широко использованы при доработке ряда урановых месторождений отрасли. Они могут быть с успехом использованы в горной промышленности и при добыче других полезных ископаемых.
К настоящему времени в России имеется единственное действующее уранодобывающее предприятие АООТ "Приаргунское производственное горно-химическое объединение (ППГХО)", отрабатывающее традиционным способом Стрельцовскую группу урановых месторождений в Забайкалье.
В целях повышения эффективности работы предприятия был выполнен ряд технико-экономических исследований и проектных проработок, на основе которых произведены переоценка и экономическая классификация запасов. В результате выделена активная часть запасов, которая может быть рентабельно отработана комплексным способом, включающим в себя горно-химическую технологию и традиционную горно-металлургическую добычу и переработку.
При комплексной отработке запасов предусматриваются добыча и переработка богатых руд с применением систем разработки, обеспечивающих минимальные потери и разубоживание, с последующей переработкой добытых руд на гидрометаллургическом заводе, а руд со средним содержанием горно-химической технологией, предусматривающей выщелачивание урана из замагазинированной руды в блоках и на поверхности в кучах (штабелях).
В 1990 1991 годах на предприятии были начаты опытно-промышленные работы по кучному выщелачиванию балансовых руд с содержанием урана 0,15 %. В результате удалось получить извлечение урана в раствор 60 80 % в зависимости от содержания, литологического состава и величины куска руды. Дальнейшими работами было установлено, что площадки для кучного выщелачивания целесообразно сооружать не на рудниках, а непосредственно на территории ГМЗ. Это позволяет одновременно выщелачивать большие объемы руды и направлять продуктивные растворы на переработку непосредственно на ГМЗ, минуя стадию твердофазной регенерации и получения кристаллов АУТК (аммоний уранил трикарбонат) на площадках рудников.
По этой схеме на территории ГМЗ организовано кучное выщелачивание урана проектной производительностью до 500 тыс. т выщелоченной руды в год.
При комплексной отработке Стрельцовской группы месторождений вышеназванными технологиями предусматривается значительно улучшить технико-экономические показатели предприятия.
|