Николай Богатов Доктор экономических наук
Россия давно и устойчиво занимает первое место в мире по запасам и добыче природного газа. В 1990 году из ее недр извлечено 640,3 млрд. м3 "голубого топлива". За пять последующих лет добыча уменьшилась на 13 %. Это не результат проблем газовой промышленности, а следствие просчетов в осуществлении экономической перестройки. По прогнозной оценке, общие запасы газа составляют 236 трлн. м3, из них 61,2 трлн. м3 переведены в запасы открытых и доказанных месторождений. В предшествующие годы всего добыто 9,5 трлн. м3 природного газа, и, следовательно, открытых и перспективных запасов достанет на многие десятилетия. Наиболее перспективными считаются регионы Восточной Сибири и акватории северных морей.
В России создана самая мощная в мире газотранспортная система, соединяющая воедино все месторождения стран СНГ. Газ доставляется также в дальнее зарубежье. На начало 1997 года протяженность газопроводов составила 146,7 тыс. км. Их структура характеризуется следующими данными (см. таблицу).
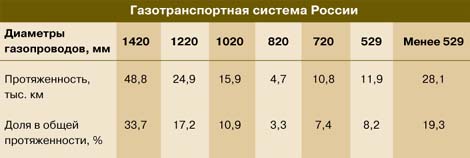 Значение каждой группы трубопроводов не одинаково. Газопроводы диаметром 1420 мм являются основными. Их суммарная проектная пропускная способность составляет более 600 млрд. м3. По ним транспортируется почти весь добываемый газ. Некоторые действующие газопроводы эксплуатируются более 25 лет, и с каждым годом газопроводов, которые выработали свой временной ресурс, будет все больше и больше.
Для нормального обслуживания действующих и строительства новых газовых магистралей необходимы надежные поставки труб диаметром 1420 мм. Российские заводы таких не изготовляют. На украинских металлургических комбинатах и трубных заводах в свое время было создано производство листовых штрипсов и труб диаметром 1420 мм суммарной мощностью 1800 тыс. т в год. Теперь РАО "Газпром" вынуждено всю свою потребность в трубах 1420 мм удовлетворять за счет импортных закупок. Абсолютная зависимость "Газпрома" от импорта опасна. Политические разногласия России со странами-поставщиками могут привести к эмбарго на поставку труб. Прецедент уже создан в 60-е годы так поступила Западная Германия.
Таким образом, следует признать, что организация производства отечественных труб диаметром 1420 мм является первостепенной государственной задачей. В ее решении должны принять активное участие РАО "Газпром", металлургические комбинаты и трубные заводы России, а их действия координироваться правительственными органами.
Создавая производство труб 1420 мм, необходимо исходить из объективных требований к их качеству. Импортные трубы такого диаметра достаточной надежностью и долговечностью не обладают. По этой причине имеют место отказы в работе газопроводов. Поэтому организация производства труб 1420 мм должна не повторять зарубежные технологические схемы, а представлять собой крупный шаг в развитии металлургического и трубного производства.
Геометрические размеры и механические свойства труб считаются отработанными. Анализ строительства и эксплуатации газопроводов показывает, что при оценке труб следует применять принципиально новые критерии и показатели:
способность основного металла труб и сварного шва противостоять коррозии, ведь именно из-за недостаточной устойчивости к ней происходит большинство незапланированных отказов в работе газопроводов;
высокая устойчивость материала труб против старения в процессе длительной эксплуатации в режиме циклического нагружения, что характерно для работы магистральных газопроводов. Старение металла сопровождается его охрупчиванием и увеличивает опасность хрупких, а значит, и протяженных нарушений газопроводов;
максимальная надежность изоляции труб, что может быть обеспечено ее выполнением в заводских условиях;
минимизация сварочных работ в трассовых условиях, что достигается увеличением длины труб до 18, а еще лучше до 24 м;
неразрушающий контроль труб по всему сечению после осуществления всех технологических операций изготовления труб, связанных с деформированием металла.
Придавая важное значение обеспечению потребности РАО "Газпром" в трубах 1420 мм отечественного производства, Минэкономики РФ поручил металлургическим предприятиям разработать соответствующие предложения. Комбинаты и заводы проявили завидную активность. Основные предложения следующие.
1. Создание на металлургических комбинатах непрерывной разливки слябов соответствующих размеров, строительство толстолистового стана 5000 и трубоэлектросварочного цеха мощностью около 1 млн. т прямошовных (с одним швом) труб в год.
2. Создание на ОАО "Челябинский трубопрокатный завод" (ЧТПЗ) производства двухшовных труб с термомеханической обработкой сварных швов. Изготовление двухшовных труб предполагается из листа производства ОАО "НОСТА" на стане 2800 после его реконструкции.
3. Создание на ОАО "Производственное объединение "Волжский трубный завод" (ВТЗ) производства спиральношовных труб с толщиной стенки 15,7 мм (первый этап) с последующим ее увеличением до 20 25 мм.
Предложенные варианты существенно отличаются друг от друга по затратам, времени реализации и особенно по качеству труб.
Вариант организации производства одношовных труб со строительством толстолистового стана 5000 и трубоэлектросварочного цеха на одном металлургическом комбинате (непременное условие из-за труднорешаемых и дорогостоящих проблем транспортировки листа шириной 4500 мм и длиной 18000 мм по железной дороге) наименее предпочтителен из-за высокой стоимости (до 1,5 млрд. долл.), чрезмерно больших объемов строительно-монтажных и пуско-наладочных работ, на которые потребуется 10 12 лет. Кроме того, и это особенно важно для служебных свойств труб, не ясны технологические приемы, с помощью которых будут устранены внутренние напряжения в готовых трубах, возникающие в процессе регулируемой прокатки листа, холодного деформирования при формовке листа и экспандирования труб с целью придания им окончательных размеров с минимальными допусками. Высокий же уровень внутренних напряжений в металле снижает коррозионную стойкость. В случае проникновения коррозийной среды к металлу труб, что неизбежно даже при незначительных повреждениях изоляции наружной поверхности газопроводов, немедленно начинается коррозия, усиленная внутренними напряжениями.
Вариант создания на Челябинском трубопрокатном заводе производства двухшовных труб с термомеханической обработкой сварных швов в техническом отношении представляет определенный интерес. Однако этот способ производства еще не вышел из стадии исследований. Необходимо их форсировать, чтобы своевременно обеспечить сравнительные комплексные испытания этих труб с одношовными и спиральношовными термообработанными трубами.
Прежде чем перейти к оценке предложений ВТЗ по организации производства труб 1420 мм, остановимся на вопросах выбора конструкции труб для сооружения магистральных газопроводов. Нормативы Американского нефтяного института (APJ) на изготовление труб для нефтяной и газовой промышленности общепризнаны в мировой практике. В этих нормативах нет подразделения труб по способу их производства прямошовные или спиральношовные. Возможность применения определяется только реальными потребительскими свойствами, которыми обладают те или иные трубы.
Спиральношовные трубы нашли широкое применение в зарубежной практике строительства нефте- и газопроводов в самых различных условиях равнинной и гористой местности в густонаселенной Европе (в Германии, Англии, Голландии, Италии, Норвегии, Швейцарии, Бельгии, Польше, Чехии, Словакии и др.), болотистой местности с участками грунта вечной мерзлоты в Северной и Южной Америке (США, Канаде, Аргентине, Перу), в пустынях Азии и Африки (Кувейт, Алжир, Нигерия и др.). Спиральношовные трубы укладываются на самых ответственных участках по дну рек, озер и морей. Диаметры построенных нефте- и газопроводов из спиральношовных труб от 529 до 1220 мм, а рабочее давление достигает 100 атмосфер. Всюду они работают надежно, обладают необходимой долговечностью. Длительная практика строительства и эксплуатации таких трубопроводов не выявила каких-либо недостатков, присущих исключительно спиральношовным трубам.
Тем не менее в России все еще существует предубеждение по отношению к ним. Дело в том, что в начале 60-х годов на Ждановском металлургическом комбинате было организовано производство газопроводных спиральношовных труб. Еще продолжалось освоение технологических процессов, качество рулонной стали было невысоким, процессы формовки и сварки еще не обеспечивали надлежащего качества, контроль сварных швов неразрушающими методами отсутствовал, но уже решили приступить к строительству газопроводов из этих труб. А далее произошло то, что и должно было произойти: газопровод не выдержал внутреннего давления. Разрушение имело лавинообразный характер, протяженность разрыва составила около 2500 м.
Отметим, что лавинообразные разрушения газопроводов имели место и в других странах. В частности, в Северной Америке зафиксированы два случая лавинообразного разрушения газопроводов из прямошовных труб протяженностью 10000 и 12500 м. В то время для изготовления труб применяли металл с низкими вязкими свойствами. Хрупкое состояние металла в совокупности с большой энергией сжатого газа внутри трубопровода и обуславливали протяженный характер разрушений. Они стали не поводом для признания труб непригодными для магистральных газопроводов, а сигналом к тщательному исследованию и устранению причин, вызвавших лавинообразные разрушения.
Так же поступили, начиная производство спиральношовных труб, волжские трубники и липецкие металлурги изготовители рулонной стали. В результате интенсивных исследований технологических процессов на ОАО "НЛМЗ" были разработаны оптимальные скорости непрерывной разливки стали, отработаны режимы нагрева и прокатки слябов, смотки и охлаждения рулонов. Почти в 5 раз увеличена длина ленты в рулоне. Серповидность ленты была минимальной, а точность ее ширины и толщины не вызывала нареканий.
В свою очередь волжские трубники разработали системы автоматического управления всеми основными процессами формовки ленты и труб, осуществили ультразвуковой и рентгено-телевизионный контроль сварного шва. Был создан и освоен процесс термической обработки труб по всему сечению. Сегодня на ВТЗ стабильно работает единственный в мире процесс термической обработки труб для нефте- и газопроводов. Вместо плазменной резки концов внедрена обработка резанием. Освоена технология трехслойной изоляции наружной поверхности труб единственная в России. Внедрена сквозная, начиная от рулонной стали, система пооперационного контроля качества труб в полном соответствии с международными требованиями. Впервые в мировой практике освоена система оценки качества труб неразрушающими методами по всему сечению, когда технологические операции по изготовлению уже завершены.
Волжские трубники совместно с различными НИИ продолжают поиск путей улучшения качества труб и объективной оценки их реальных служебных характеристик. Совсем недавно новая серия комплексных испытаний труб была проделана Нижегородской НИЛИМ. Особенность этого исследования состояла еще и в том, что оно проводилось одновременно по единым методологическим принципам как для спиральношовных, так и для прямошовных труб. Что же показали испытания? Прямошовная труба до разрушения выдержала 1627 циклов нагружения, а спиральношовная 4407 циклов, т.е. в 2,7 раза больше. Кроме того, проведены статические нагружения труб до разгружения с предварительным нанесением искусственных дефектов в виде надрезов длиной 450 мм. Прямошовная труба разрушилась при 60 барах (расчетное разрушающее давление 60,4 бар). Спиральношовная труба при расчетном разрушающем давлении 63 бара была нагружена давлением 100 бар, но разрушения не произошло. Вторичное нагружение спиральношовной трубы до 100 бар также не вызвало ее разрушения. И только после углубления искусственного дефекта труба разрушилась при давлении 77 бар, а расчетное разрушающее давление с учетом углубленного надреза составило 44 бара. Статическая трещиностойкость спиральношовной трубы оказалась в 1,7 раза больше, чем у прямошовной.
С учетом изложенного утратили свою актуальность постоянные дискуссии о пониженном качестве спиральношовных труб из-за большей протяженности сварных швов по сравнению с одношовными трубами. Сварной шов у спиральношовных термообработанных труб никогда не является слабым местом.
Более высокое качество спиральношовных труб по сравнению с прямошовными подтверждается их фактическим состоянием после длительной эксплуатации. На нефтепроводе Лазарево Нижний Новгород после длительной эксплуатации обследовали два участка один из спиральношовных труб длиной 203,3 км, а другой из прямошовных протяженностью 225,7 км. Оба участка находились в одинаковых условиях эксплуатации. Проверкой внутренней поверхности спиральношовных труб выявлено 603 случая поверхностных отслоений металла, а прямошовных 2961 случай, т.е. в 4,9 раза больше.
Подводя итог, отметим, что мы не отдаем явного предпочтения ни одному из названных выше вариантов. Его выбор ввиду особой важности проблемы должен носить в высшей степени объективный и доказательный характер. Что касается обеспечения РАО "Газпром" другими видами труб, то здесь проблем существенно меньше.
На Волжском трубном заводе имеется электросталеплавильный цех мощностью около 1200 тыс. т. в год, который оборудован всеми видами внепечной обработки стали с полной компьютеризацией технологических процессов. Здесь есть условия для выплавки стали любого химического состава, а значит, проблему ее получения для качественных труб можно считать решенной. В металлургическом комплексе предусмотрено производство труб на непрерывном стане в диапазоне диаметров 168 426 мм. Цех оснащен оборудованием для прокатки и термообработки (по любому режиму) труб, их нарезке и всестороннему контролю качества. Проектная мощность цеха составляет 720 тыс. т труб в год. Однако в настоящее время производственные мощности по выплавке стали и производству труб используются менее чем на 20 %. При заинтересованности и завода, и потребителей должны быть найдены решения для загрузки этого производства. Инвестиции здесь окупятся в течение года, учитывая экономию валютных средств, широко используемых для закупки труб по импорту.
Работа металлургического комплекса ОАО "ВТЗ" в проектном режиме полностью обеспечит потребности в трубах диаметром до 529 мм не только РАО "Газпром", но и всех нефтяников России. А трубы в диапазоне диаметров 529 1020 мм на полную потребность РАО "Газпром" могут быть изготовлены Выксунским металлургическим заводом, имеющим соответствующие производственные мощности в 1 млн. т в год. Чтобы полностью исключить изоляцию выксунских труб в трассовых условиях, следовало бы набраться сил и реализовать совместное решение завода и РАО "Газпром" о создании здесь участка заводской изоляции.
Мощности по выпуску труб диаметром 1220 мм имеются в избытке на ЧТПЗ. В ближайшее время челябинские трубники самостоятельно введут в действие отделение изоляции труб в заводских условиях.
Чтобы качество труб в диапазоне от 529 до 1220 мм соответствовало требованиям РАО "Газпром", металлургическим комбинатам ОАО "Северсталь" и ОАО "НОСТА" необходимо завершить уже начатую работу по повышению технического уровня листовых штрипсов на толстолистовых станах 2800.
|