Валерий Паршин, Игорь Рапопорт ГНЦ РФ "ЦНИИчермет им И.П. Бардина" ООО "Модуль-Инжиниринг"
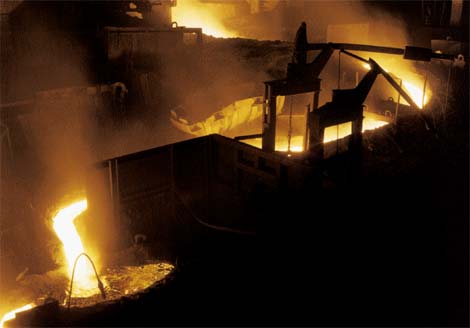 Сегодня уже, наверное, мало кто помнит события середины 60-х годов, когда нынешние "законодатели мод в металлургии" японцы приезжали в Липецк учиться и снимали на кинокамеры процесс непрерывной разливки стали. Зато хорошо известно, что именно Россия была одной из первых стран мира, где в промышленном масштабе была реализована идея бесслитковой прокатки, высказанная еще в конце прошлого столетия Генри Бессемером. Эти работы были начаты в конце 30-х годов академиком А.А. Целиковым в МВТУ им. Баумана и в лаборатории завода "Серп и молот", а затем получили мощное развитие в творческом коллективе под руководством академика И.П. Бардина. Итогом этих работ стал пуск в середине 60-х годов конвертерного цеха, в то время одного из самых совершенных в мире, на Липецком металлургическом комбинате.
В последующие годы российскими металлургами были разработаны и внедрены такие прогрессивные новшества в технологию непрерывной разливки (сегодня ее часто называют процессом непрерывного литья заготовок), как установка шибера в сталеразливочном ковше, применение разливки "под уровень", создание специальных огнеупорных изделий, изменение схемы расположения технологической оси процесса от вертикальной и криволинейной до горизонтальной, что, безусловно, подтверждает весьма высокий научно-технический потенциал российской металлургии.
К сожалению, были приостановлены поисковые исследования по созданию агрегата для прямого получения литой полосы из жидкой стали, проводимые в 50 60-х годах в ЦНИИчермет им. И.П. Бардина, по причине отсутствия в тот период необходимой технической базы.
К достижениям мирового класса следует отнести также создание одной из первых промышленных установок, совмещающей литье и прокатку в составе агрегата УНРС, планетарный стан для производства катанки, который успешно работает на Электростальском заводе уже более 20 лет.
Как теряли приоритет
Золотым веком непрерывной разливки стали в мировой черной металлургии можно смело назвать 70-е и начало 80-х годов, когда был осуществлен мощный количественный и качественный прорыв в развитии этой технологии. За 1980 1995 годы удельный вес стали, разливаемой непрерывным способом, в среднем в мире возрос с 28 до 70 %.
Трудно объяснить, почему в нашей стране вопреки мировым тенденциям прогресса в этот период один за другим сооружаются сталеплавильные цехи на крупнейших комбинатах (Карагандинском, Западно-Сибирском, Ждановском им. Ильича, Днепродзержинском) с традиционным способом разливки в слитки, а строительство отделений непрерывной разливки отодвигается на более далекую перспективу. Только в начале 80-х годов удалось изменить техническую политику в отрасли (что в значительной степени связано с именем С.В. Колпакова), и планы ускоренного развития непрерывной разливки получают партийную (тогда это было равносильно государственной) поддержку, приобретая силу закона. В результате программы развития предприятий начинают учитывать новейшие тенденции в развитии процесса и поэтому предусматривают возможность "горячего" или "теплого" посада заготовок. Значительные средства получает отраслевая наука для форсированного решения текущих и перспективных задач в области техники и технологии непрерывной разливки стали. Широко разворачиваются работы по совмещенным процессам, валковым и другим суперсовременным видам непрерывной разливки.
К сожалению, эти меры запоздали: распад СССР, положивший конец существованию единого металлургического комплекса страны, рыночные реформы, довольно болезненные и не во всем последовательные, реорганизация отраслевой системы управления, инвестиционный кризис и почти полное прекращение финансирования все это надолго приостановило научно-технологическое обновление металлургического производства.
На пороге XXI века технический уровень существующего парка МНЛЗ России замер на рубеже 70 80-х годов века уходящего.
В настоящее время на территории России в мартеновских, конвертерных и электросталеплавильных цехах работают 60 МНЛЗ различных типов суммарной мощностью около 29 млн. т/год.
Следует отметить, что парк МНЛЗ листового назначения в основном физически изношен и морально устарел (ККЦ-1 и 2 АО "НЛМК", ККЦ АО "Северсталь") и в сравнении с аналогичными зарубежными цехами грешит излишним количеством агрегатов.
Технический уровень МНЛЗ для получения сортовых заготовок более высок, однако и они по многим параметрам не соответствуют современным требованиям (АО "Носта", АО "КМК", АО "Амурсталь", АО "ОЭМК").
Характерной особенностью отечественных МНЛЗ является сравнительно низкий уровень их автоматизации.
В то же время разработанная технология и действующее оборудование позволяют производить заготовки квадратного, прямоугольного и круглого сечения для производства сортового проката (строительного и машиностроительного сортамента), труб, колес, бандажей, проволоки из углеродистых, низколегированных, легированных и высоколегированных марок сталей; горячекатаные и холоднокатаные лист, полосу и штрипс для судо- и котлостроения, газо- и нефтепроводов, сосудов, работающих под давлением, мотостроения, электротехнической и автомобильной промышленности, кинескопной ленты, строительной индустрии, бытовых товаров и т.д. из углеродистых, качественных, низкоуглеродистых, низколегированных, легированных, высоколегированных, электротехнических и других марок сталей.
Необходимость изменений диктует рынок
Не секрет, что металлопродукция российских заводов по многим параметрам ценовой конкурентоспособности существенно уступает зарубежным аналогам. Если анализировать структуру себестоимости, то, например, удельные затраты энергоресурсов в России почти в 1,6 раза превышают уровень, достигнутый в странах с развитым рыночным хозяйством. Аналогичное положение сложилось и с другими составляющими себестоимости, за исключением, пожалуй, лишь затрат на оплату труда и ремонтные нужды. Такое положение в значительной степени объясняется техническим отставанием российской металлургии, в частности, сталеплавильного передела. Это отставание ведет к огромному росту издержек производства либо вообще лишает нашу страну технической возможности производить многие необходимые виды металлургического сортамента, что усиливает экономическую зависимость страны от внешнего рынка.
К таким видам металлопродукции относятся в первую очередь:
толстый лист, в том числе крупногабаритный для судостроения, высокопрочный для изготовления некоторых видов продукции для нефтегазового и оборонного комплексов;
электротехническая сталь, в том числе массового назначения, с высокой магнитной проницаемостью;
металлопрокат коррозионностойкой стали разного назначения, в частности, для атомной энергетики и производства бытовой техники;
рельсы длинномерные (до 50 м) для магистральных железных дорог;
жесть белая (толщиной 0,15 0,22 мм) для пищевой промышленности;
высококачественная кордовая катанка.
На российских предприятиях есть отдельные современные производства, но нет ни одного завода, где были бы сосредоточены все необходимые переделы для производства указанных видов продукции. Например, высококачественную литую заготовку для толстого листа может производить ряд предприятий (КЦ АО "НЛМК", ЭСПЦ АО "Северсталь"), однако современного толстолистового стана нет в России вообще. Аналогичное положение характерно и для производства рельсов мирового качества. Только АО "ОЭМК" может производить литую заготовку, высочайшее качество которой доказано неоднократно.
Выходом из этого положения может быть широкая кооперация между предприятиями, но она маловероятна в условиях России из-за высоких транспортных издержек и других, в том числе внеэкономических, причин.
Отдельные положительные примеры кооперации, конечно, не могут изменить общую довольно безрадостную картину, но тем не менее их следует отметить. В частности, на базе Магнитогорского металлургического комбината и Верх-Исетского металлургического завода с использованием оригинальной технологии, разработанной в АО "ВИЗ", отрабатывается производство до 160 тыс. т в год электротехнической анизотропной стали нитридного варианта выплавки. Эта продукция имеет низкую стоимость и повышенный экспортный потенциал, обладает высокими потребительскими свойствами. Так, по электромагнитным характеристикам она приближается к стали с высокой магнитной проницаемостью, которая выпускается элитными производителями и в 1,6 раза дороже, чем традиционные виды электротехнической стали. По экспертным оценкам, осуществление такого проекта закрепит отечественный приоритет в качественно новом виде продукции и даст значительную прибыль.
Ряд российских металлургических предприятий, сумев получить заемные средства либо используя собственные, начал структурную перестройку. Однако, насколько известно, принятые на этих предприятиях решения не содержат по-настоящему новых технологий, в первую очередь модульных. Это объясняется тем, что стратегия технического перевооружения большинства предприятий в основном формировалась в 70 80-е годы, и технологические подходы многих руководителей в целом соответствуют тому времени. Длительный застой в этом вопросе привел к тому, что сегодня даже решения о реконструкции отдельных участков или цехов могут быть неверными, так как исходят из устаревших концепций развития предприятия. Кроме того, нынешняя финансовая ситуация во многом предопределяет скорее поиск способов выживания, чем разработку долгосрочной стратегии развития.
Технологическая революция с помощью модуля
Основой для резкого (не менее чем на 30 %) снижения производственных затрат должно стать использование модульных технологий.
В широком плане под модульными технологиями можно понимать совмещение технологических операций как минимум на двух смежных переделах, функционирующее на организационных принципах единого агрегата, для производства конкурентоспособной продукции с минимальными затратами. Возникновение модульных технологий принципиально возможно только на базе самых современных достижений в области получения металлургического сырья, сталеплавильного и прокатного производств, потенциальные возможности которых, в свою очередь, полностью реализуются только в модульном исполнении. Это является основой того, что сегодня именуется "технологической революцией" в мировой металлургии и обретает зримые черты в США, Германии и других странах.
В литературе достаточно полно освещены принципы работы и оборудования модульных технологий в основном на стадии "сталь прокат" получение на промежуточном этапе литой заготовки, максимально приближенной к конечным размерам. Наряду с листовыми модулями здесь имеются модули для производства сортопроката, катанки и т.д. Перспективными являются модули для производства толстого листа, являющегося основой для изготовления трубных и нержавеющих марок стали. Следует отметить, что и при традиционных процессах непрерывной разливки отмечаются тенденции к уменьшению размеров сортовых заготовок и слябов.
Форма совмещения весьма обширна (совмещение прокатки сорта и листа с термической обработкой после прокатки; травления и прокатки и т.д.). При этом, кроме снижения затрат, достигаются два важных результата: изменение микроструктуры металла и улучшение свойств, а также создание предпосылок для получения более универсального ряда марок сталей при определенной "санации" существующих ГОСТов и технических условий.
Для структурной перестройки черной металлургии в определенной степени мог быть полезен зарубежный опыт. Прежде всего имеются в виду страны, где "большая металлургия" была создана сравнительно недавно (Юго-Восточная Азия, Латинская Америка), а также страны с традиционно развитой металлургией на базе классического технологического цикла "доменная печь кислородный конвертер МНЛЗ прокатный передел" (США, Западная Европа). Основу успешного развития мировой металлургии составляют следующие направления.
1. Ориентация на производство стали в электродуговых печах, технико-экономические показатели работы которых за последние 30 лет улучшились в несколько раз. При этом наряду с ростом производительности и оптимизацией энергозатрат удалось существенно повысить качество стали, уровень экономической безопасности и культуры труда.
В российской металлургии использование электропечей как наиболее эффективных агрегатов по выплавке стали, к сожалению, не вызывает оптимизма.
2. Развитие технологии непрерывной разливки, где четко просматривается применение установок, обеспечивающих максимально возможную гибкость по размерному и марочному сортаментам продукции, а также низкие эксплуатационные расходы и капиталовложения. Такое положение наблюдается в последние годы в производстве сортовой и в особенности листовой продукции, где результаты особенно ощутимы.
3. Развитие технологий и оборудования совмещенных литейно-прокатных модулей; появление одноклетьевых листовых станов горячей прокатки листов и полос требуемого качества; новых конструкций прокатных клетей и другого оборудования для производства сортового проката; комплексных мини-заводов для производства холоднокатаной листовой стали на базе процессов CSP и JSP.
Современные концепции непрерывной разливки, технологии и оборудования для станов, выпускающих прутки и катанку, современных станов новой конструкции для прокатки листов и полос широкого сортамента, мини-заводов по производству холоднокатаной листовой продукции, выпуск которой открывает широкие возможности для выхода на региональный потребительский рынок (профилированный настил, гнутые профили, электросварные трубы, метизы и многое другое), открывают большие возможности для начала структурной перестройки российской металлургии практически по всем направлениям производства металлопродукции.
Принятие решений в конце 90-х годов уже не связано с технологическим риском такого масштаба, как это было десятилетие назад: новые технологии убедительно доказали свое право на существование, а переориентация на мини- и макропроизводства является оптимальным и экономичным способом развития черной металлургии.
Стратегия модернизации каждому предприятию
Успехи, достигнутые мировыми производителями оборудования и разработчиками технологий для литья тонких полос, пригодных для дальнейшей холодной прокатки, настолько значительны, что у специалистов нет сомнений в том, что через 2 3 года произойдет очередной прорыв в этой области.
Новые технологии и новая организация производства на металлургических заводах позволяют радикально изменить ситуацию в черной металлургии благодаря их чрезвычайной гибкости и доступности по уровню капитальных затрат. В настоящее время основными факторами, определяющими размещение мини-завода, являются доступность сырья и энергоносителей, а также наличие рынка сбыта продукции.
Российские заводы, специализирующиеся на выпуске холоднокатаной листовой стали и не имеющие собственного производства заготовки, могли бы с большим интересом рассмотреть возможность строительства установок литья тонких полос и тем самым реанимировать свои предприятия. В первую очередь это относится, по нашему мнению, к Верх-Исетскому и Ашинскому металлургическим заводам, Миньярскому метизному заводу, Московскому металлургическому заводу "Серп и молот" и некоторым другим.
Пожалуй, наиболее близким примером перехода к решительной модернизации и структурной перестройке можно считать черную металлургию США. Еще 20 лет назад она отставала по уровню технологии от металлургии ФРГ и Японии. В настоящее время только на предприятиях нового типа производится до 40 % конкурентоспособной продукции. Это свидетельствует о том, что инвестиционная и техническая стратегия в данном случае базируется на использовании современной технологии совмещенных процессов, облекаемых в форму мини-заводов.
Стратегические решения по модернизации российских предприятий либо строительству отдельных производств, интегрируемых в действующие, должны проходить тщательную экспертизу с проверкой соответствия требованиям технологической и организационной структуры мини-завода в новом понимании. Можно без глубокой проработки привести ряд примеров гипотетического характера такого подхода в условиях России. В частности, на базе электросталеплавильного цеха ь 6 АО "Мечел" после выполнения ряда реконструктивных мероприятий можно организовать производство конкурентоспособной листовой продукции, в том числе из коррозионностойких сталей с использованием современных технологий.
Еще большие перспективы для структурной перестройки металлургического производства и поэтапного превращения в предприятие с современной технологией имеет Оскольский электрометаллургический комбинат. Исключительные возможности сырьевой базы и генплана позволяют ему успешно реализовать производство высококачественного сортового проката, листовой продукции и даже современных рельсов на базе модульных технологий при условии реконструкции, например, стана 700.
Все изложенное в той или иной мере применимо к другим предприятиям черной металлургии России. Например, проблема изготовления сортового проката различных профилеразмеров на основе современной технологической схемы может быть решена на базе модернизированного сталеплавильного оборудования ЭСПЦ АО "Северсталь" с приданием этому производственному комплексу статуса мини-завода.
Другие возможные примеры: строительство мини-комплексов на основе модульных технологий на металлургических заводах АО "Алапаевский" и АО "Лысьвенский".
Возможны возражения оппонентов против, например, предложения построить на модульном принципе листовое производство в АО "ОЭМК" и в Белгородской области вообще, так как в непосредственной близости находится крупнейший производитель листа АО "НЛМК". Однако следует иметь в виду, что модульный принцип производства позволяет сократить на четверть эксплуатационные затраты, т.е. в этих условиях выигрывает тот, кто применяет новую технологию.
Учитывая богатый зарубежный опыт, экспертные оценки и конкретные программы модернизации российских металлургических предприятий, мы считаем, что в современных условиях приоритет должен быть отдан инвестиционным проектам, в основу которых положены модульные технологии.
Сегодня практически на любом металлургическом предприятии России можно реализовать стратегию модернизации на вышеизложеннных принципах, так как имеется гамма технологий, принципиальная схема которых по существу универсальна. Схема поэтапного выхода на современные технологии позволяет максимально использовать действующие агрегаты и цехи, последовательно выводя устаревшие и не останавливая производства в целом. Легче привести примеры исключения из правил, когда металлопродукция не может быть получена по такому принципу.
Трудно переоценить значение модульных технологий в техническом перевооружении и реструктуризации отрасли, так как при этом решаются следующие важные технико-экономические задачи:
реструктуризация крупных металлургических предприятий на базе модернизации существующего электросталеплавильного производства путем интеграции в него модульных технологий на переделе "непрерывная разливка стали прокатный стан" (АО "Мечел", АО "Северсталь");
строительство мини-комплексов на новых площадках (Белгородская область, завод "Севморпуть" г. Мурманск);
модернизация существующих сталеплавильного или прокатного производств путем объединения их на основе модульных технологий (АО "Белорецкий металлургический завод", АО "Дальневосточный металлургический завод");
реструктуризация металлургических и машиностроительных заводов небольшой мощности путем сооружения литейно-прокатных комплексов (АО "ПО Усольмаш", АО "Алапаевский металлургический завод", АО "Петрозаводскмаш").
Реализацию таких проектов целесообразно осуществлять с участием зарубежных фирм, обладающих хорошими возможностями в выборе оборудования и технологическим опытом его освоения.
Безусловно, стратегия технического перевооружения предприятий прерогатива их владельцев. Но те или иные виды государственной поддержки (гарантии, налоговые льготы и т.д.) следует оказывать лишь тем предприятиям, которые следуют государственной стратегии развития экономики страны, обеспечивая ее экономическую безопасность.
Для этого необходимо:
разработать модель стратегии структурной перестройки отечественной металлургии, содержащей данные по объему, сортаменту выпускаемой продукции и экономически выгодным объектам их производства (на базе действующих или новых);
предусмотреть применение на этих производствах новейших технологий, включая бездоменную металлургию, электросталеплавильное производство, совмещенные (разливка прокатка) процессы с применением современных видов прокатных станов (например, получение горячекатаного листа толщиной менее 1 мм, технологическое объединение горячей и холодной прокатки и пр.);
финансировать комплексные отечественные научные разработки, соответствующие или превышающие мировые уровни (получение литой ленты и прутка непосредственно из жидкой стали).
В нашем понимании, модель стратегии структурной перестройки отечественной металлургии должна быть разработана в дополнение к Федеральной программе развития отрасли. Но в ее реализации в не меньшей степени будут заинтересованы и регионы.
|