Владимир Денисов, Георгий Кулешов, Елена Звекова
Газообразный диоксид серы, образующийся при переработке сырья и сжигании топлива, является одним из самых распространенных загрязнителей окружающей среды. Проблема очистки газов с содержанием SO2 порядка 0,01 1,0% достаточно сложна, т. к. разработанные и применяемые в настоящее время технологии либо не позволяют полностью решить вопросы экологической безопасности (продукты обессеривания сбрасываются в отвалы и не подлежат утилизации), либо требуют больших затрат (адсорбционные и электронно-лучевые процессы). Вот почему в последнее десятилетие большое внимание отечественными и зарубежными исследователями уделяется использованию для этих целей газовых разрядов различных форм.
Институтами Гинцветмет и Высоких температур Российской Академии наук (ИВТАН), рядом других организаций разработан и проходит испытания комплексный метод очистки сбросных газов сернокислотных цехов заводов цветной металлургии от диоксида серы и аэрозоля серной кислоты с использованием импульсно-частотного стримерного разряда с получением продукта очистки в виде серной кислоты, используемой в технологическом цикле основного производства. Метод заключается в превращении SO2 в H2SO4 под действием стримерного импульсно-частотного разряда (70 КВ, 500 нс, 3 4 КГц) с дальнейшим улавливанием в этом же аппарате аэрозоля серной кислоты. При этом превращение SO2 в H2SO4 происходит с эффективностью 90%, а степень улавливания аэрозоля серной кислоты составляет не менее 99% при энергозатратах 3 4 Вт. ч/м3 очищаемого газа.
По сравнению с известными химическими и радиационными методами очистки серосодержащих газов данная технология обладает рядом преимуществ. Она позволяет в одном аппарате переводить серосодержащие компоненты в серную кислоту и улавливать их в виде серной кислоты, не требует специальных химических реактивов и защиты от ионизирующих излучений. Система легко адаптируется к существующим технологическим схемам.
Процесс осуществляется в аппарате, выполненном по типу мокрого электрофильтра (см. рисунок), оснащенного импульсно-частотным генератором и имеющего специальную конструкцию коронирующих электродов.
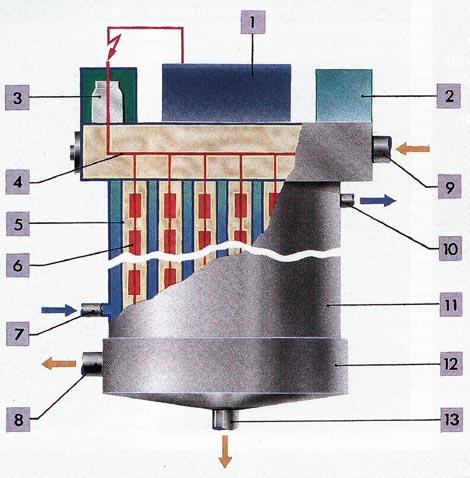 | 1 импульсно-частотный генератор 2 изоляторная коробка 3 опорно-проходой изолятор 4 штанга подвеса коронирующих элементов 5 осадительый элемент 6 коронирующий элемент 7 вход охлаждющей воды 8 выход газа 9 вход газа 10 выход охлаждающей воды 11 корпус аппарата 12 бункер 13 слив кислоты |
Для осуществления процесса в межэлектродном промежутке генерируются импульсы высокой частоты, под действием которых происходит процесс окисления SO2 в H2SO4. Реакция проходит на поверхности или внутри аэрозольных частиц, образовавшихся в результате бинарной нуклеации серной кислоты и воды, и состоит из следующих стадий:
растворение SO2 в поверхностном слое аэрозольной частицы;
диффузия растворенного SO2 во внутрь частицы;
диссоциация растворенного SO2;
химическая реакция SO2 с растворенным окислителем.
Оценка характерных времен указанных выше стадий гетерогенного окисления SO2 показывает, что лимитирующей стадией является взаимодействие диоксида серы с растворенным в капле окислителем. На кинетику процесса сильно влияют температура и влажность газа. Характерное время процесса составляет долю секунды. Степень эффективности в конечном итоге определяется количеством и способом внедрения энергии в разрядный промежуток.
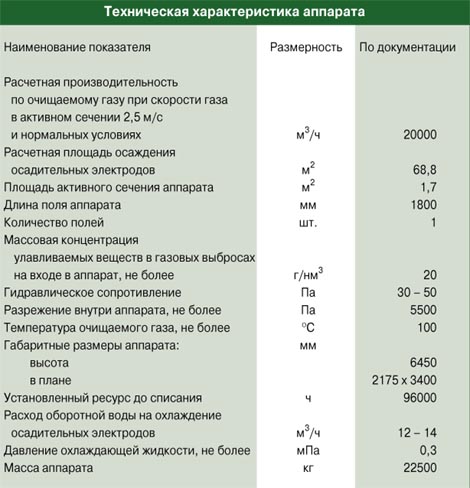
В процессе проведения исследований разработаны помехоустойчивые методики диагностики импульсно-частотного разряда, позволяющие определять импульсное напряжение, длительность импульсов напряжения и тока, а также частоту следования импульсов. Создан и испытан блок регистрации электрических импульсов, позволяющий изучать корреляционные соотношения между электрическими параметрами и эффективностью технологического процесса.
Разработана и испытана на модельных и реальных промышленных газах схема импульсно-частотного питания с использованием высоковольтных коммутаторов, позволяющая в широких пределах согласовывать нагрузку с источником первичного напряжения и осуществлять как формирование импульсов, так и режим суммирования импульсного и постоянного напряжения при независимом регулировании их величины и полярности. В результате в технологическом режиме повышена стабильность, снижена вероятность пробоев, уменьшена критичность по напряжению и снижены требования к центровке электродов. Разработан блок импульсно-частотного источника питания для установки производительностью 20 тыс. нм3/ч.
На основе совместных исследований института Гинцветмет и ИВТАН по этому принципу был построен и испытан ряд пилотных установок производительностью 4000 м3/ч на технологических газах различных производств (серосодержащие газы обжига медных, никелевых и молибденитовых руд). Создан проект и ведется монтаж установки производительностью 20 тыс. нм3/ч на Челябинском электролитном цинковом заводе.
u u u
Важным этапом явился поиск путей интенсификации процесса конверсии за счет изменения конструкции электродной системы аппарата. Испытаны разнообразные конструкции электродов как с точки зрения эффективности конверсии и улавливания, так и по длительности их эксплуатации в агрессивных газовых средах в условиях высоких энергий электрического поля. Предполагается в дальнейшем внести изменения в конструкцию промышленных аппаратов: возможно значительное уменьшение габаритных размеров установки, что положительно скажется при внедрении аппаратов производительностью по газу 40 — 60 тыс. нм3/ч.
Предлагаемая технология использования специального электрического поля позволяет очищать технологические газы не только от серосодержащих компонентов, но также от оксидов азота с переводом их в азотную кислоту и от органических соединений. Аналогичные аппараты могут быть использованы для очистки газов, содержащих ртуть, селен, мышьяк и др. К настоящему времени технология запатентована.
Технология была представлена на двух международных выставках, состоявшихся в Республике Корея и в Норвегии. Ведутся переговоры о заключении контрактов на строительство установок с рядом зарубежных фирм.
Экономические сведения о состоянии и перспективах реализации проекта:
Стадии, которые необходимы для реализации проекта в полном объеме:
а) проектирование и согласование проекта 4 мес.
б) изготовление и монтаж аппарата 6 мес.
в) пуско-наладочные испытания 3 мес.
|