Анатолий Сысоев Генеральный директор Богословского алюминиевого завода
В своей работе мы исходим из постулата: все определяют люди. Предприятие может развиваться лишь в той мере, в какой оно развивает таланты своих работников и поощряет их творческую отдачу. Успеха в конкурентной борьбе можно добиться, если делаешь сегодня то, о чем другие начнут думать только завтра. В любом деле системная, отлаженная работа обыкновенных людей в итоге приносит больший эффект, чем случайные озарения гениев.
Нашей команде вот уже 15 лет удается работать вместе без особых изменений в кадровом составе. Выработана система, определены принципы, подходы. Мы создаем работникам предприятия нормальные условия для труда и отдыха. Мы также думаем о школах, о развитии детей, о спорте, культуре, здоровье, жилье, проведении праздников.
Единственно значимое конкурентное преимущество Богословского алюминиевого завода его инженеры, техники и рабочие. Очень многое зависит от их знаний, квалификации, и многими нашими достижениями мы обязаны именно этим людям. И впредь нам следует гармонично сочетать интересы работников предприятия, жителей города и акционеров компании.
Прежде, чем поделиться некоторым опытом работы Богословского алюминиевого завода, приведу краткую историческую справку. Тем более это уместно в год юбилея отечественной алюминиевой промышленности.
Первый камень в строительство нашего завода был заложен 11 октября 1940 года. Первоначально планировалось на нем производить:
глинозема 100 тыс. т;
алюминия 15 тыс. т.
В последующем утвердили новые проектные задания:
глинозема 930 тыс. т;
алюминия 152,5 тыс. т.
Зимой 1941 1942 годов начались основные работы по строительству завода, а 17 июня 1943 года уже выдали первую продукцию гидроксид алюминия.
17 апреля 1944 года получен первый глинозем.
9 мая 1945 года выдан первый алюминий.
К 1980 году производство достигло:
глинозема 1100 тыс. т,
алюминия 152,5 тыс. т,
анодной массы до 150 тыс. т,
алюминиевых порошков до 17 тыс. т.
До 1986 года активно шел процесс интенсификации, однако к 1987 году на заводе накопились очень серьезные проблемы, которые выразились в недостатке незавершенного производства, расстроенной технологии.
В 1988 году начался первый этап восстановления нормального технологического процесса, создание инфраструктуры, нормальных условий труда и жизни работников. Наш завод расширялся: строились новые объекты, приобретались предприятия, которые практически были банкротами (мы восстанавливали их экономику и производственный цикл).
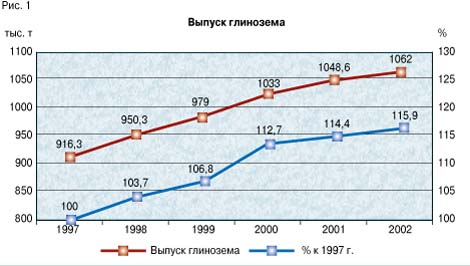 Глиноземное производство БАЗа в 1987 1988 годах испытывало серьезные трудности. Разрушенные здания, низкая производительность выпарного, автоклавного переделов, кальцинации, печей спекания, высокие расходные коэффициенты, высокая доля фракции 45 мкр.
Сегодня мы решили проблему кальцинации, спекания, выпарных батарей по производительности, произошло укрупнение грансостава, снижены расходные коэффициенты. Введено новое оборудование: АТК-слой, поршневые насосы. Здания, которые требовали ремонта, большей частью (70 %) восстановлены.
Производство глинозема увеличено с 930 тыс. т (проектная мощность) до 1060 тыс. т. Однако есть еще много нерешенных проблем. Среди них высокий уровень расхода энергоресурсов (25 мгДж у нас, против 17 мгДж на зарубежных заводах). Пока не достигнута достаточная стабильность по грансоставу глинозема, содержание фракции 45 мкр выше 20 %, a-фаза выше 10 %. Остается низкой производительность печей кальцинации, которые требуют коренной реконструкции. В ряду других проблемы следует отметить слабое использование информационных технологий, отсутствие гарантированной системы сбыта глинозема и гидрата. Практически не внедряем давно испытанные эффективные аппараты большой мощности выпарные, автоклавные батареи, печи кальцинации, декомпозеры, сгустители, промыватели.
Тем не менее в последние 5 8 лет мы искали лучшие решения по интенсификации производства алюминия. Ведь в наших технологиях есть особенности, которые предопределяют эффективность всех прочих технических организационных мер. Вот мы и задались целью в корне пересмотреть наши взгляды на весь процесс производства алюминия от кремнепреобразовательной подстанции до движения металла в сторону литейного отделения.
На первом этапе мы решили проблему качества анодной массы с учетом технических решений в ЦАМе; перехода на "сухую" анодную массу с низким содержанием оксида натрия, золы; общей разрушаемости. Таким образом, нам удалось достичь энергетической стабилизации.
Второй важный элемент технологии это способность электролита хорошо растворять глинозем. Ошибка многих ученых и специалистов-практиков, работающих в отрасли, состоит в недооценке этой проблемы. Электролизники-технологи всегда пытались решить эту задачу только за счет качества глинозема, за счет укрупнения грансостава и снижения a-фазы и не обращали внимания на свойства электролита. Сегодня анализ работ западных ученых показывает, что за счет качества электролита можно добиться улучшения растворимости глинозема на 25 30 %, а за счет технологических решений в электролизе более чем в 2 раза.
Ранее мной проводились большие работы на электролизерах алюминия высокой частоты, где были всегда значительные зашлаковывания электролитов. Тогда мои решения привели к исключению шламообразования. Основываясь на своих расчетах, предложил своим технологам состав электролита, который обеспечивал лучшую растворимость глинозема в условиях стабильного энергетического режима с более высокой плотностью тока. Требовалось поднять температуру перегрева, снизить температуру плавления электролита, не увеличивая при этом температуру процесса. Мы приняли меры к увеличению теплопотерь в случае подъема температуры электролита за счет подъема уровня металла и электролита до 35 см и 20 см соответственно и использования фланцевого листа особой конструкции как теплонасоса.
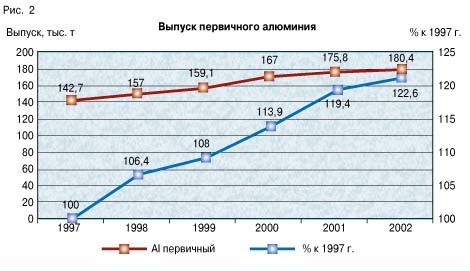 Результаты превзошли все ожидания. Температура электролита снизилась с 960 до 949 952 оС, температура перегрева повысилась в 2 раза, электролизеры запросили поднятия тока и повышения его плотности. В течение одного-двух месяцев исчезли "коржи", осадки. Сформировались новые формы настылей. Одновременно с подъемом тока начал расти выход по току. Не стало ванн с расстроенным ходом. С учетом всей предыдущей работы мы добились одинаковых параметров на всех электролизерах серий по уровню металла, электролита, составу электролита.
Были выполнены укрупненные электрические балансы по каждому электролизеру, определено падение напряжения в междуполюсном расстоянии, которое было установлено на всех электролизерах, равное 3200 мВт. Зная падения напряжения на остальных участках цепи, установили рабочее напряжение на системе "Электра-160".
Стабилизация энергетического режима позволила сократить частоту обработки в 1,5 2 раза при той же частоте вспышек 0,5 0,7 в сутки.
Повышение выхода по току привело к уменьшению прихода тепла за счет вторичных реакций. Произошли изменения в конструкции электролизера. Мы отказались от искусственных настылей, применили усиленные катодные кожухи с днищем, в качестве подовой массы использовали холодно-набивную массу КрАЗа. Внедрен газовый обжиг подин с пуском на электролите. Все это позволило сократить время простоя в капремонте в 2 раза и довести до 12 суток, увеличить срок службы электролизеров до 56 58 месяцев.
В результате освоения комплексной интенсивной технологии электролиза алюминия произошло суммарное уменьшение электросопротивления анодного и катодного узлов на 13,9 %, при этом на долю анода приходится 75 %, и 25 % эффекта достигнуто за счет улучшения состояния подины, катодных спусков, системы охлаждения, катодной ошиновки.
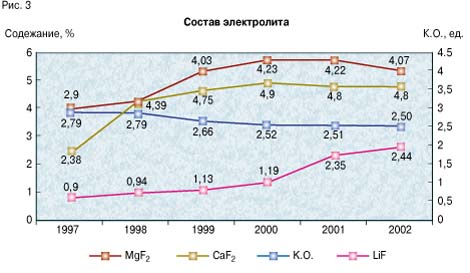 Таким образом, получены следующие результаты.
1. Достигнуто классическое распределение избытка энергии между полезными затратами и тепловыми потерями (по ~ 50 %), возможное только при правильном ведении процесса интенсификации. По прежнему опыту интенсификации на других заводах основная доля увеличения прихода энергии затрачивалась на тепловые потери.
2. Улучшилось расположение изотерм, определяющих форму рабочего пространства и эксплуатационную стойкость катода. Объем электролита в пространстве борт-анод увеличился в 1,8 2 раза, что имеет большое значение для снижения кратности обработки.
3. Выявлена особая роль анода в выносе тепла из междуполюсного зазора. Анод является своеобразным тепловым насосом, снижающим температуру электролита и градиент температуры между центральной зоной междуполюсного зазора и периферией. В ходе интенсификации эта роль существенно возросла, что обеспечило увеличение резервов повышения силы тока и выхода по току.
4. Достигнуто постоянство температуры электролита и междуполюсного расстояния в ходе интенсификации при значительном увеличении прихода тепла означает высокую степень стабилизации теплового баланса, достигнутую в результате внедрения следующих основных организационно-технических мероприятий.
5. Эффективная работа АСУТП, новая система измерения тока по принципу Холла, использование совершенных алгоритмов управления. Погрешность системы меньше 0,2 %. Отклонения среднего значения тока за смену не более 0,01 кА от заданного, за сутки не более 0,01 кА.
6. Достигнута стабилизация технологических параметров в установленных нормативами узких диапазонах является самостоятельным мощным средством стабилизации теплового баланса.
7. Усовершенствована система диагностики технологического состояния электролизеров серии, основанная на оперативном контроле падения напряжения в междуполюсном зазоре, анодном и катодном узлах, междуполюсного расстояния, температуры и состава электролита, параметров анодных эффектов, "шумов" в спектре рабочего напряжения.
8. Поточная обработка представляет собой мощный источник дестабилизации теплового режима. Конструктивные особенности электролизеров БТ в совокупности с главными составляющими ИТЭ обеспечивают возможность снижения кратности обработки. Осуществлен переход от 8-кратной обработки к 6-кратной. В настоящее время ведутся испытания 4-кратной обработки.
9. При увеличении уровня металла с 27 до 35 см и объема электролита в пространстве борт анод повысилась тепловая инерционность электролизера, при этом подъем уровня металла, в отличие от общеизвестного практического опыта, сопровождался уменьшением длины подовой настыли, толщины осадка и полным исключением коржей при использовании мелкозернистого глинозема песчаного типа собственного производства.
10. Исключение искусственной настыли способствовало сохранению бортового гарниссажа, увеличило резервы теплового саморегулирования, улучшило условия подпитки электролита глиноземом из осадка, снизило плотность горизонтальных токов в металле и электросопротивление подины.
11. В результате внедрения вышеперечисленных мероприятий реализован важнейший принцип интенсификации, обеспечивающий необычно большой прирост производительности одновременное повышение силы тока и выхода по току. Попытки увеличения производительности серии за счет повышения силы тока без внедрения технологических и организационных мер по повышению выхода по току, как показывает обширный промышленный опыт, обычно приводят к обратному результату. Увеличение силы тока на 1,5 % (максимально достигаемое) сопровождается, как правило, снижением выхода по току до 2 %, ухудшением состояния технологии и увеличением расходных коэффициентов.
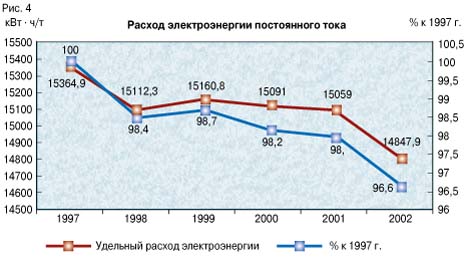 Завод поднял силу тока на 7,4 % и повысил выход по току на 5 %. Это уникальный случай в российской металлургической промышленности. В этой технологии у нас есть определенные тонкости и особенности. Не все можно повторить один к одному, в то же время есть решения, которые должны обеспечить большую эффективность.
Наша работа требует не только самоотверженного труда, но и творческого подхода к делу. К примеру, у нас есть идеи, которые надо ускоренно внедрять: точечное питание глиноземом; создание электролизного производства как системы, стабильной по времени. Для этого следует дорабатывать программное обеспечение, максимально автоматизируя процесс. Человек в нем должен играть роль наблюдателя.
Очень важно делать анализ того, что получилось. Еще важней того, что не получилось. Надо прогнозировать, с какими проблемами мы столкнемся, как будут развиваться основные тенденции в экономике страны и мира, какой будет наша ниша на рынке в будущем. Уже сейчас мы должны искать ответы на следующие вопросы:
будем ли конкурентоспособны завтра, через год, через 10 лет;
что будет влиять на себестоимость продукции, и в какой мере;
во что мы должны вкладывать деньги (прежде всего, вероятно, в амортизационное обеспечение, снижение энергозатрат, повышение производительности труда, новые научные исследования и разработки);
устраивает ли нас структура заводов, уровень подготовки технологов, ремонтников, соотношение инженеров и рабочих?
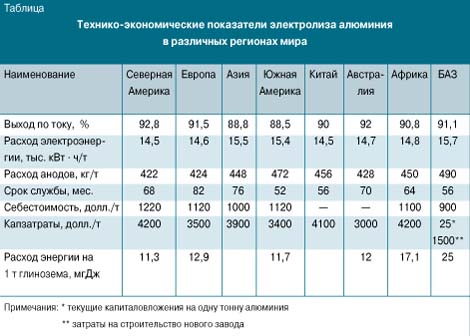 Очень важный вопрос отношение к людям, их квалификации, здоровью, социальным проблемам. Мы, управленцы, создаем единую команду. Коллектив как семья. Негоже думать, что нам нужна только прибыль, а остальное проблемы трудящихся. Уверен, человеческий фактор все больше и больше будет играть роль в конкурентной борьбе.
В то же время не следует уходить от выполнения функции лоббирования. Мы должны следить за законотворчеством, политикой правительства и формировать ее в направлении, способствующем эффективной работе наших предприятий.
Готовится постановление Правительства РФ по реструктуризации металлургического комплекса. В мире перепроизводство стали, алюминия, меди и других металлов. В российской металлургии предполагается сократить численность работающих на 350 тыс. человек.
Вхождение в ВТО ужесточит конкурентную борьбу, не все смогут ее выдержать. Реструктуризация естественных монополий и настойчивость руководства ВТО, добивающегося, чтобы в России стоимость газа, электроэнергии, железнодорожных перевозок поднялась до мировых значений, приведут к многократному росту тарифов. Многие промышленные предприятия просто перестанут существовать. Требуется серьезно осмыслить будущую ситуацию. Необходимо успеть разработать и внедрить комплекс мер, обеспечивающих выживание отраслей.
Если мы хотим, чтобы в будущем у нас было меньше подобных острых проблем, мы уже сейчас должны найти пути их решения и двигаться с опережением.
|