Юлиан Юсфин
Профессор, доктор технических наук
Николай Пашков
Профессор, доктор технических наук
Московский государственный институт стали и сплавов
Cегодня 95 % стали производится двухступенчатым способом: в доменных печах из руды получают чугун, а из него, добавляя лом, производят сталь в конвертерах, мартеновских печах, электросталеплавильных агрегатах. Такая технологическая схема, сложившаяся почти 150 лет назад, отличается высокой производительностью, низким расходом ресурсов, разнообразием продукции. Но инженерный ум не мирится с громоздкой и внешне противоречащей здравому смыслу технологией: на первой стадии (восстановление оксидов железа и некоторых попутных элементов) получение сплава, насыщенного углеродом и содержащего избыточное количество кремния, а в ряде случаев марганца, хрома и др., на второй (окисление углерода, кремния и др.) плавка стали требуемого химического состава. Итог долгих поисков выплавления стали из железной руды в одном агрегате "прямого получения железа" отражает убеждение подавляющего числа специалистов в бесперспективности подобных исследований. Это соответствует логике совершенствования инженерного труда дроблению сложных процессов на отдельные операции и доведению каждой из них до высокой степени эффективности. Сегодня совершенно ясно, что по прямому пути получения железа мы придем к крайне неэффективному и ресурсно избыточному способу выпуска продукта низкого качества.
Однако опыт научных поисков не пропал даром, трансформировавшись в решение задачи иного рода замену доменной печи как производителя первичного металла. Домна является исключительно эффективным производственным агрегатом. Ее характеризует значительная степень извлечения железа (99 % и выше), низкий расход ресурсов, особенно энергетических, а также высокая производительность и сравнительно малые выбросы в окружающую среду. Доменная печь имеет лишь два крупных ограничения, которые создают ряд трудно решаемых проблем, а для отдельных стран и регионов делают использование классической металлургической схемы чрезмерно дорогой, а то и полностью невозможной. Это, во-первых, необходимость проплавки шихты определенного кускового состава и, во-вторых, применение в качестве основного энергоносителя исключительно каменноугольного кокса. Поскольку подавляющая часть добываемой из недр руды представлена мелкими пылеватыми фракциями, требуется специальная операция окускование, отличающаяся значительным расходом энергии и, к сожалению, значительными выбросами твердых частиц в атмосферу.
Кроме того, запасы коксующихся углей в мире ограничены, а во многих странах отсутствуют вовсе. При этом коксохимическое производство уязвимо в экологическом плане. Поэтому для многих стран использование вместо доменной печи альтернативного агрегата основное условие развития национальной металлургии.
Наряду с этим следует также учитывать и другие факторы:
стремление более рационально использовать топливно-энергетические ресурсы, возможность увеличить в черной металлургии долю газа, нефти, некоксующихся углей;
ограниченность ресурсов скрапа гарантированной чистоты и стабильного состава;
возможность достижения более высокого качества стали при использовании для ее выплавки металлизованного сырья вместо скрапа (известно, что металлизованное сырье отличается чистотой по вредным примесям, особенно по цветным металлам);
возможность организации маломасштабной металлургии (мини-заводов) и расширения экономико-географических регионов рентабельного металлургического производства на основе получения и использования металлизованного сырья, что для многих развивающихся стран крайне важно.
Процесс внедоменного получения металла, который, порой, по-прежнему именуют "процессом прямого получения железа", не более, чем дань традиции. На самом деле, это вариант двухступенчатых процессов, разделенных на два больших класса: твердофазные и жидкофазные. В твердофазных процессах отнятие кислорода от оксидов железа газообразным или твердым восстановителем происходит при температурах ниже расплавления компонентов шихты. Продукт восстановления называется губчатым железом или металлизованными окатышами. В высокотемпературном процессе восстановление железа происходит при температуре плавления оксидной и металлической фаз.
Чаще всего губчатое железо применяют как высокочистую добавку к стальному лому при плавке в электропечах, а также для его замены в случае дефицита или высоких цен. Наиболее стабильный спрос на губчатое железо отмечается в странах с недостаточными мощностями доменного передела и ресурсами стального лома. Меньшую роль в производстве металла губчатое железо играет в промышленно развитых странах Европы, в Японии и США, где железная руда, стальной лом и твердое топливо продолжают оставаться относительно дешевыми.
Основными, используемыми на работающих, строящихся и проектируемых установках для производства губчатого железа, являются процессы с применением шахтных печей (главным образом, процесс "Мидрекс", ХиЛ-III) и реторт периодического действия (процесс ХиЛ-I и ХиЛ-II). Отметим, что для шахтной печи, как и для доменной, необходимо окускованное сырье. Процессы с использованием вращающихся печей и твердого восстановителя (СЛ-РН, "Крупп-Айзеншвам", "Кавасаки" и др.) в последние годы находят некоторое промышленное применение, главным образом, при переработке металлургических отходов пылей и шламов, которые содержат примеси цинка, свинца и др., а также комплексных руд (богатых титаном, хромом, никелем, марганцем и др.), не пригодных для использования в доменных печах. Вращающиеся печи могут использовать пылеватое рудное сырье, но уязвимы с позиции современных экологических требований.
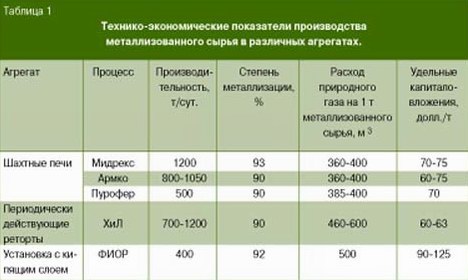
Процессы в кипящем слое получили меньшее распространение в связи с целым рядом специфических особенностей (жесткие требования к гранулометрическому составу, газодинамические ограничения существования кипящего слоя, температурные условия и др.). Преимущественное развитие в мировой практике процессов "Мидрекс" и ХиЛ с получением губчатого железа обусловлено их лучшими технико-экономическими показателями (табл. 1). В настоящее время на долю "Мидрекс" и ХиЛ приходится около 80 % производства металлизованного сырья в мире, в том числе на "Мидрекс" 60 65 %. В России этот процесс реализован на Оскольском электрометаллургическом комбинате (ОЭМК).
Установки внедоменного получения железа сооружаются в основном в развивающихся странах, с относительно малой потребностью рынка в стали, ограниченными капиталами, малыми ресурсами лома и коксующихся углей и большими ресурсами железной руды и природного газа.
При оценке перспектив развития процессов бездоменной металлургии, основанных на замене чугуна губчатым железом, следует иметь в виду следующие обстоятельства.
Процессы получения металлизованных окатышей происходят в твердофазной области без образования шлака. Поэтому пустая порода не удаляется. Это относится и к попутным элементам. При увеличении количества пустой породы в металлизованных окатышах их проплавка в электропечах сопровождается ростом потерь железа со шлаком, а, главное, существенным ростом расхода электроэнергии. Опыт плавки губчатого железа в электропечах показал, что экономически приемлемо получение стали из металлизованных окатышей при наличии в последних не более 3 % пустой породы. Таким образом, первым условием производства губчатого железа в шахтных печах металлизации является наличие богатых или легкообрабатываемых руд.
Качество стали зависит от содержания в ней примесных элементов серы, фосфора, хрома, никеля, других цветных металлов. Поэтому вторым условием, которое необходимо учитывать при производстве губчатого железа, является чистота перерабатываемых руд по примесным элементам. Для большинства руд и концентратов, используемых для получения металлизованных окатышей, содержание фосфора не превышает 0,02 0,04 %, серы менее 0,02 %, суммарное содержание цветных металлов менее 0,02 %. Состав руд и окисленных окатышей, применяемых для получения губчатого железа, приведен в таблице 2.
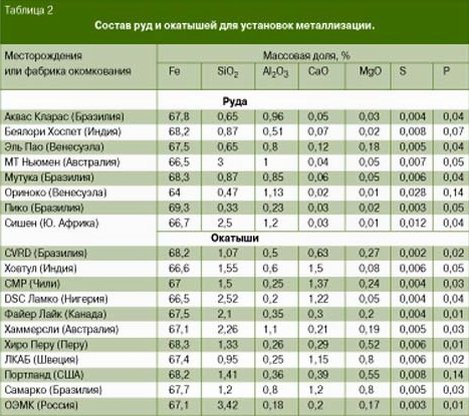
В шахтных печах металлизации для восстановления оксидов железа применяется газообразный восстановитель. В настоящее время его получают путем воздушной, углекислотной или паровой конверсии природного газа. В зависимости от типа конверсии или их комбинации получают газ-восстановитель, содержащий в определенной пропорции монооксид углерода и водород. Так, восстановительный газ для шахтных печей металлизации ОЭМК содержит 30 32 % СО, 55 58 % Н2, 2 3 % СО2, 5 6 % Н2О, около 3 % СН4, 2% N2.
Учитывая, что процессы газификации твердого и жидкого топлива еще ждут своих разработчиков, в ближайшей перспективе получение газа-восстановителя возможно в основном из природного газа. Итак, третьим условием применения процесса металлизации железорудного сырья в шахтных печах металлизации является наличие запасов природного газа. Неудивительно поэтому, что строительство заводов бездоменной металлургии активно ведется в странах Ближнего Востока и Латинской Америки, а также в Индонезии.
Промышленный опыт получения губчатого железа показал, что этот процесс сопровождается двумя важными особенностями, не имеющими значения для доменной плавки. Первая из этих особенностей сваривание окатышей или кусков руды при их восстановлении в шахтных печах. Образующееся в твердофазной области свежевосстановленное железо выделяется в виде очень мелких включений, обладающих избыточной поверхностной энергией, спекающей мелкие частицы. Под давлением верхлежащих слоев восстановленные окатыши свариваются в своеобразные "гроздья", которые нарушают газораспределение, снижают скорость восстановления и теплообмена и тем самым обуславливают получение некондиционной продукции. Сваривание подавляют, снижая температуру в печи. В шахтных печах она, как правило, меньше 800 850 оС, что определяет низкие скорость процесса и производительность агрегата. Ни одна из промышленных шахтных печей металлизации не достигла производительности 1 млн. т продукции в год. Обычное годовое производство 400 600 тыс. т, т.е. на порядок меньше мощной доменной печи.
Другая особенность процесса получения губчатого железа опасность вторичного окисления. При наличии в окружающей среде окислителя (даже воздуха) уже упомянутое стремление металлизованных окатышей снизить избыточную поверхностную энергию зерен металла легко реализуется окислением железа. Способность свежевосстановленного железа к самовозгоранию именуется пирофорностью. Известны случаи полного сгорания железнодорожных вагонов и морских судов, транспортировавших губчатое железо. Особенно активируется окисление и горение металлизованных окатышей в присутствии водяных паров.
Склонность металлизованных окатышей к окислению или, как ее именуют, реакционная способность металлизованных окатышей зависит как от температуры восстановления и степени металлизации, так и от температуры, при которой происходит окисление железа. По лабораторным данным, металлизованное водородом при 500 оС губчатое железо загорается на воздухе через несколько секунд. При низкотемпературном восстановлении и степени металлизации меньше 85 % окатыши загораются в крытом складе через 6 8 часов, тогда как при степени металлизации меньше 90 % они в этих же условиях хранятся очень долго. При высокотемпературном восстановлении (больше 880 оС) окатыши со степенью металлизации 80 % на открытой площадке не загораются, даже политые водой.
Как изменяется реакционная способность (RB) металлизованных окатышей, восстановленных при разных температурах, показано в таблице 3. Кроме того, скорость окисления металлизованного продукта зависит от температуры, при которой он хранится.
Итак, чтобы не допустить свариваемости окатышей, следует снижать температуру в печи, а для подавления пирофорности губчатого железа ее необходимо повышать. Эти ограничения обуславливают сложность при выборе параметров режима.
Качество металлизованных окатышей весьма влияет и на расход ресурсов в электропечи при их проплавке, и на качество стали. Для губчатого железа степень металлизации обычно колеблется в пределах 87 97 %. Низкие степени металлизации (87 89 %) применяются при использовании высокофосфористых руд и для получения необходимой окисленности шлака при деформации металла в процессе расплавления губчатого железа.
Практикой установлено, что с целью использования высокой мощности трансформаторов электропечей и предохранения футеровки стен и сводов от воздействия электрических дуг плавление металлизованных окатышей должно сопровождаться вспениванием шлака за счет реакции окисления углерода. При этом толщина шлакового слоя на ванне металла увеличивается в четыре-пять раз и экранирует электрические дуги. Создать такой шлаковый режим можно, вдувая в ванну газообразный кислород, а в случае его отсутствия добавляя окисленные окатыши или применяя металлизованные с пониженной степенью металлизации. Такая технология некоторое время применялась на ОЭМК, однако это вело к повышенному расходу электроэнергии при расплавлении.
Расчеты и опыт показывают, что с повышением степени металлизации с 90 до 94 % удельный расход электроэнергии на расплавление 1 т металла снижается примерно на 18 кВт . ч на каждый процент металлизации.
Оптимальным содержанием углерода в металлизованном продукте, предназначенном для получения стали, является такое, которое достаточно для восстановления оксидов железа металлизованных окатышей и науглероживания металла до требуемых пределов. Это важно при выплавке ответственных марок стали, так как углерод окатышей по сравнению с углеродом других науглероживателей, особенно кокса, не содержит вредных примесей. Кроме того, в настоящее время стоимость углерода, полученного из природного газа, значительно меньше, чем из кокса. В некоторых случаях выгодно иметь в губчатом железе большое (до 3,5 %) содержание углерода. Выжигание 3 % углерода кислородом во время плавления губчатого железа позволяет экономить до 50 кВт . ч/т жидкой стали. На установках металлизации ОЭМК производят металлизованные окатыши с содержанием углерода 0,5 2 % по требованиям заказчика.
Мировое производство металлизованного сырья в 1997 году составляло 31,2 млн. т. В 2005 году выпуск железа прямого восстановления составит 53 млн. т. Развивается мировой рынок товарного металлизованного сырья. В 1995 году 7,6 млн. т железа прямого получения перевезено по суше и морю в регионы с отрицательным балансом чистой металлошихты. По оценке, мировая потребность в металлизованном сырье к 2005 году стабилизируется на уровне 27 29 млн. т. Наличие хорошего рынка говорит о перспективности инвестиций в этот металлургический передел.
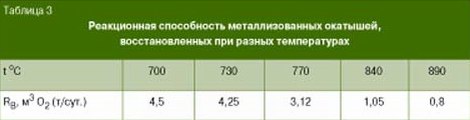
Переход к строительству мини-заводов полного цикла на основе производства губчатого железа наметился еще в 70-х годах. Это связано с тем, что при соизмеримой энергоемкости схема "шахтная печь электропечь" имеет следующие преимущества:
меньший эффект масштаба. Схема "домна-конвертер" экономически эффективна, как правило, при производстве 3 млн. т стали в год, а схема "шахтная печь электропечь" уже при 300 400 тыс. т в год;
более низкая стоимость основных фондов. Капитальные затраты на схему "домна конвертер" и "шахтная печь электропечь" составляют, соответственно, 750 и 380 долл./т непрерывнолитой заготовки;
меньшая потребность в рабочей силе. При мощности завода 1 млн. т первичного металла этот показатель составляет 2,6 и 1,2 чел./ч на тонну для схем "домна конвертер" и "шахтная печь электропечь", соответственно;
возможность быстрого ввода мощностей в течение 20 месяцев с начала строительства.
Производство губчатого железа в мире росло в 90-е годы быстрыми темпами, достигнув в 1997 году 37 млн. т против 15,8 млн. т в 1989 году. Затем темпы роста существенно снизились. Так, в 1998 году прирост составил только 4,1 %, а загрузка производственных мощностей, которая в 1996 году равнялась 88 %, упала до 82 %. Тем не менее, сохранился высокий уровень инвестиций в создание мощностей по производству продукта прямого восстановления. За последние два года эти мощности увеличились на 7,5 млн. т, или на 20 %, и, несмотря на то, что ряд проектов был отменен или отложен, рост, вероятнее всего, продолжится. В ближайшие годы будут введены мощности еще на 10 млн. т.
В конце 80-х годов в мировой металлургии утвердились бездоменные технологии производства жидкого металла, которые обычно объединяют термином "жидкофазные процессы". В промышленном варианте используется процесс "Корекс", разработанный в ФРГ и действующий в ЮАР, Южной Корее и Индии. Агрегат для производства чугуна представляет собой доменную печь, разрезанную пополам. Верхняя часть домны используется как шахтная печь, где до высоких (около 90%) степеней металлизации восстанавливается окускованный материал (агломерат, окисленные окатыши, кусковая руда). Во втором агрегате (нижняя часть доменной печи горн) металлизованные окатыши плавятся, металл науглероживается, причем топливом является кусковой уголь, сжигаемый в токе кислородного дутья, а газ, получающийся в результате неполного горения, является восстановителем.
Главным преимуществом этой технологии является замена кокса недефицитными видами угля. Основные недостатки высокий расход энергоносителей (в 1,5 2 раза выше, чем в доменной печи), потери попутных элементов со шлаком, невозможность получения литейных чугунов и ферросплавов и неясные экологические последствия. Заметим, что при реализации технологии "Корекс" преодолевается одно из ограничений доменной плавки происходит замена кокса углем, но не решается задача исключения из традиционной металлургической схемы этапа окускования руд. Видимо, по этим причинам процесс "Корекс" не находит широкого распространения.
Привлекательнее, на наш взгляд, выглядит разработанный в России процесс "Ромелт", позволяющий получать из неокускованной руды и угля жидкий чугун в одном агрегате. Особенно выгодна эта технология при переработке техногенного сырья и газификации углей. В настоящее время ведется проектирование завода с применением этой технологии для Индии.
Практика последних десятилетий позволяет утверждать, что бездоменная металлургия железа существенно расширила возможности и нашла свою нишу в мировой металлургии. Для развитых стран это производство высококачественного металла. Для регионов, богатых природным газом, это металлургия широкого профиля, но ограниченных объемов, зависящих в основном от качества железорудного сырья. Для стран, не обладающих запасами коксующихся углей и не богатых газом, это в основном жидкофазные процессы, обеспечивающие минимальные потребности в железе.
Вместе с тем большинство специалистов склоняется к мнению, что традиционная и альтернативная технологии производства стали не конкурируют, а в большей степени дополняют друг друга, причем объем бездоменных способов получения стали, видимо, стабилизируется, составив в перспективе 10 20 % ее мирового производства.
|