Александр Гречко
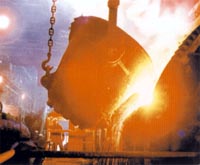 | Заливка расплава из ковша в агрегат (старая технология) |
Крупномасштабное производство металлов в черной и цветной металлургии это миллионы тонн чугуна, стали, меди, никеля в год. Это доменные и мартеновские печи, сталеплавильные конвертеры в черной металлургии; отражательные и шахтные печи, медеплавильные конвертеры, обеднительные электропечи в цветной. Кроме того, здесь надо назвать плавку сырья в электрических (рудно-термических, ферросплавных) печах, рафинирование чугуна, стали, меди в печах, реакторах, ковшах. Все это многообразие агрегатов и установок, отдельные из которых насчитывают уже более чем столетнюю историю, работает в периодическом режиме: плавка сырья набор расплава, выпуск расплава переливание в другой агрегат, очередная технологическая операция выпуск расплава и т.д. Для этого проводятся: периодическое открывание (бурение, пробивание, прожигание) выпускных отверстий (шпуров, леток); транспортировка расплава в емкостях (ковшах, чашах, миксерах) с помощью кранов, на тележках от одного агрегата к другому; выбивание из пустых ковшей "корок" застывшего расплава, их складирование, возврат в плавильный агрегат...
Такова типичная картина на современном металлургическом заводе. Она сопровождается постоянными разговорами о тяжелом труде при обслуживании основных агрегатов и вспомогательного оборудования, о тепловом излучении от выпускаемых и транспортируемых расплавов, о большой загазованности атмосферы на рабочих площадках и в цехах в целом, о потерях металлов между операциями и т.д.
Многие из этих проблем снимаются при переходе от периодического режима работы агрегатов к непрерывным пирометаллургическим технологиям. Увы, мечты о непрерывных процессах, о заводах-автоматах, к сожалению, пока остаются мечтами.
В черной металлургии так называемые САНДы (сталеплавильные агрегаты непрерывного действия), в свое время активно разрабатывавшиеся и в нашей стране, и за рубежом, остались на стадии полупромышленного и опытно-промышленного освоения и не получили практического распространения. Однако цветная металлургия оказалась впереди черной. В нашей стране была создана печь плавки в жидкой ванне (ПЖВ, с 1987 года разработка получила название "печь и процесс Ванюкова" ПВ).
Конструктивно печь ПВ (см. рисунок) представляет собой высокую кессонированную шахту, оборудованную отопительно-дутьевыми устройствами (газо-воздухо-кислородные фурмы, топки предварительного сжигания топлива) для продувки (барботажа) расплава. Загрузка сырья проводится сверху в брызговую область рабочего пространства шахты. Высокая подфурменная область расплава способствует разделению жидкой ванны на фазы: легкую (шлак) и тяжелую (металлосодержащий продукт). Эти фазы расплава выводятся непрерывно из печи по специальным сифонным переточным устройствам, расположенным по торцевым сторонам шахты, в поворотные миксеры-накопители. Технологические газы отводятся через газоход (аптейк) на своде печи и направляются на теплоутилизационную установку и далее в систему пылегазоочистки.
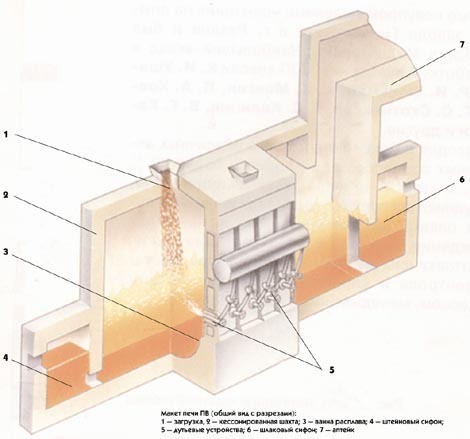 Отработка этой технологии на первых этапах велась на трех полупромышленных установках ПЖВ: на Норильском (НГМК) и Балхашском (БГМК) комбинатах и на Рязанском опытно-экспериментальном металлургическом заводе (РОЭМЗ) института "Гинцветмет". Динамика ввода печей в работу с указанием их масштаба, начиная от этих опытных установок и кончая крупными промышленными комплексами, видна из графика. В настоящее время в промышленной эксплуатации находятся шесть печей (комплексов) ПВ на трех медеплавильных предприятиях: НГМК, БГМК и Среднеуральском медьзаводе (СУМЗ). Отметим, что опытные печи на НГМК и БГМК после выполнения программы испытаний по технологии плавки собственного медного сульфидного сырья были демонтированы, а печь ПВ РОЭМЗа в течение многих лет являлась практически опытным полигоном для решения конструктивных вопросов и отработки технологии плавки самых различных видов сырья. Установка ПЖВ (ПВ) в черной металлургии на Новолипецком металлургическом комбинате (НЛМК) продолжает оставаться опытной (работает эпизодически по мере поступления заказов на отработку технологии плавки специфических видов сырья).
По сравнению со многими существующими пирометаллургическими технологиями процесс ПВ характеризуется следующими преимуществами: непрерывностью работы агрегатов, нетребовательностью к качеству и свойствам загружаемого сырья (перерабатываются материалы как крупные, так и мелкие, как сухие, так и влажные); высокой удельной производительностью по проплаву (на порядок больше); низким пылевыносом (0,5 1,5 % от количества загружаемого материала); относительно низкими потерями цветных металлов со шлаками и др. Кроме этого, технология ПВ привела к значительному облегчению условий труда по обслуживанию плавильных агрегатов, улучшению санитарных условий на рабочих местах и оздоровлению окружающей среды.
Накопленный многолетний опыт работы печей ПВ различного масштаба (от F = 0,7 до 48 м 2 см. график) и результаты расчетно-теоретических работ по барботажным агрегатам позволяют вполне объективно и надежно определяться с параметрами и показателями работы печей для конкретных видов сырья, конкретных заводских, региональных и прочих условий и возможностей.
К настоящему времени накоплен большой промышленный опыт непрерывной переработки различного медного сульфидного сырья. Основные показатели работы крупных печей ПВ на трех предприятиях бывшего Советского Союза с этим видом сырья приведены в табл. 1. Эти показатели можно считать вполне надежными, установившимися в многолетней промышленной практике.
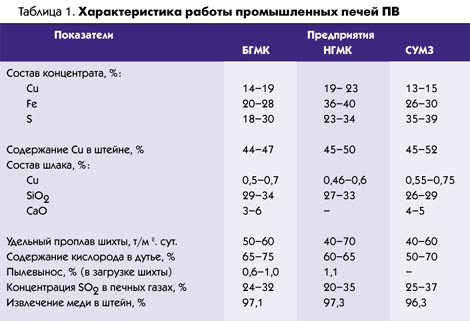
Большой объем полупромышленных испытаний по отработке технологии непрерывной переработки самых различных видов сырья проведен на РОЭМЗе. Испытания проводились большим коллективом исследователей, в основном Гинцветмета и МИСиСа; на отдельных этапах (видах сырья) привлекались сотрудники ИМиО АН Казахстана, ЦНИИОлово, НПО "Тулачермет", АКХ им. К.Д.Панфилова и др. На этой установке переработано сырье порядка 50 видов и еще более шихтовок (часть характеристик этих видов сырья приведена в табл. 2).
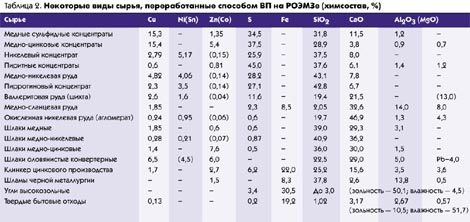 Установка на РОЭМЗе позволяет легко варьировать конструктивными и режимными вариантами и может быть приспособлена также для первоначальной отработки технологии плавки и нетрадиционных для металлургии видов материалов. Как видно из табл. 2, испытаниями была охвачена весьма широкая гамма материалов (по составам, свойствам, прочим характеристикам).
По металлургическим видам сырья подчеркнем следующее: можно считать, что в принципе отработаны технологические режимы непрерывной переработки как исходных материалов (концентратов, руд), так и получаемых при этом шлаков самого различного состава. При непрерывной обеднительной переработке шлаков, в том числе с отгонкой летучих металлов ( Zn, Pb, Sn), получены технологические показатели (извлечение металлов в товарный продукт) практически на уровне таких же показателей при периодическом режиме работы печей (отражательных, фьюминговых).
В последние годы на печи ПВ РОЭМЗа проводились испытания по переработке в непрерывном режиме в одну стадию медных и медно-цинковых сульфидных шихт на белый матт и пробные опыты на черновую (черную) медь. Получены удовлетворительные технологические результаты по первому этапу устойчивая работа печи ПВ с получением белого матта; по второму этапу получена принципиальная возможность работы на медь, но требуется продолжение отработки технологических режимов работы и конструктивных вариантов печи.
Отметим, что по удельной производительности к сульфидным видам сырья примыкают также клинкер, угли, твердые бытовые отходы, обладающие собственной теплотворной способностью (по содержанию углерода). Наряду с сульфидным сырьем переработка этих видов сырья в промышленных условиях обеспечивается в автогенном режиме при соответствующем обогащении дутья кислородом.
Особо отметим вопрос непрерывной технологии переработки нетрадиционных видов сырья на базе печи ПВ: в энергетике низкосортных (серосодержащих, высокозольных) углей, золошлаков и золоуносов современных ГРЭС и ТЭЦ, в том числе накопленных в отвалах; в коммунальном хозяйстве крупных городов твердых бытовых отходов (ТБО). В перспективе не исключена переработка и других отходов, материалов, сырья (строительные отходы, "хвосты" углеобогащения, отходы химической и нефтехимической промышленности, военно-промышленного комплекса и др.) Из опробованных в испытаниях плавки нетрадиционных видов сырья отметим, что переработка углей в барботируемом кислородсодержащим газом силикатном расплаве является решением весьма важной в энергетике проблемы. Это практически безотходная экологически чистая технология, обеспечивающая попутное извлечение металлов (Fe, Zn, Cu, Co, Ge, Pb) и использование силикатного расплава для нужд стройиндустрии (подробнее об этой технологии см. журнал "Металлы Евразии", 1996, № 3, с. 130 132).
В заключение подчеркнем, что печи ПВ и их модификации позволяют осуществить технологические схемы непрерывного процесса производства металлов в виде комбинированного агрегата или единой цепочки отдельных агрегатов. Для условий медеплавильного завода это комплекс, включающий плавку сульфидного сырья, конвертирование штейна, обеднение шлаков. В настоящее время имеются проектные проработки такого комплекса. Принцип непрерывности работы комплекса осуществляется в полном объеме по всем участкам: загрузка сырья, его плавление, перетекание из одного агрегата (или зоны) в другой, проведение очередной технологической операции, выпуск расплавов. Таким образом, мечты металлургов о заводе-автомате уже не кажутся несбыточной фантазией.
|