|
|
Журнал |
|
Архив |
|
Подписка |
|
Реклама |
|
САММИТ |
|
Книжная полка |
|
Контакты |
|
В начало |
|
|
|
| |
|
|
 |
№4' 2004 |
версия для печати
|
|
КОНВЕРТЕР В СВЯЗКЕ С ЭЛЕКТРОПЕЧЬЮ |
НОВЫЕ ВОЗМОЖНОСТИ СТАЛЕПЛАВИЛЬНОГО ПЕРЕДЕЛА |
Петр Югов
Профессор ФГУП ГНЦ РФ «ЦНИИчермет им. И.П. Бардина»
аксимально полное использование лома черных металлов в шихте сталеплавильных агрегатов остается важнейшей экономической и экологической проблемой. Ее актуальность не уменьшается даже при широком использовании заменителей лома, поскольку ресурсы этого сырья определяются размерами металлофонда страны и интенсивностью его обновления. По некоторым оценкам, запасы лома в странах с развитой экономикой ежегодно пополняются в объеме, равном примерно 30 % национального потребления стали. Это объясняется ускоренным ростом удельного веса машин и других металлоемких изделий со сравнительно быстрой амортизацией и коротким сроком службы (например, автомобилей). Не будем забывать, что на производство и чугуна, и альтернативных заменителей лома расходуются невозобновляемые природные ресурсы, а лом вторичен. Следует учитывать также, что увеличение объема амортизационного сырья ведет к накоплению экологически вредных отходов и требует огромных затрат по их утилизации.
Суммарный металлофонд стран СНГ оценивается в настоящее время в объеме около 2 млрд т, что теоретически позволяет ежегодно использовать для выплавки стали не менее 60 млн т лома. Однако значительная часть этого сырья пока реализуется на зарубежных рынках.
При использовании амортизационного лома в сталеплавильном процессе важнейшей проблемой является наличие в нем вредных примесей. Поэтому одной из главных задач является, во-первых, очистка металла от них главным образом, от цветных металлов и газов и, во-вторых, разработка технологии, позволяющей оптимально использовать химико-термические и технико-экономические преимущества основных сталеплавильных агрегатов конвертера и электродуговой печи, каждый из которых имеет свои достоинства и недостатки.
Например, конвертерный углеродистый и низколегированный металл, при выплавке которого в шихте используется большая доля чугуна, обычно чище стали, выплавляемой в электропечи, по примесям цветных металлов и содержит в 23 раза меньше азота. Последнее обеспечивает конвертерной стали большую пластичность, меньшую склонность к старению и лучшую свариваемость, что особенно важно при производстве тонкого высококачественного листа. Применение значительных количеств альтернативных заменителей лома в шихте электродуговой печи позволяет несколько снизить содержание азота в электростали (до 0,0050,006 %), но не обеспечивает этот показатель на уровне 0,0020,003 %, как в конвертере. Естественно, возникает задача: при использовании лома в доминирующих количествах добиться минимальных содержаний азота в готовой стали за счет использования новых технологий.
Сложившаяся практика конвертерного производства, его нынешняя технология позволяют перерабатывать в конвертерах от 23 до 28 % лома, в зависимости от химического состава и температуры чугуна, качества шлакообразующих материалов, сортамента выплавляемой стали и эксплуатационных характеристик технологического оборудования. При этом расчеты, а также анализ реальных условий работы конвертерных цехов показывают, что технологические возможности процесса с точки зрения увеличения доли лома, определяемые его естественным тепловым балансом, практически полностью исчерпаны. Фактически доля лома в конвертерных цехах российских заводов составила в среднем по отрасли 27,3 %.
Теоретические расчеты и экспериментальные исследования показали, что долю лома в конвертерной шихте можно повысить до 35 % и выше за счет дооборудования агрегатов и дополнительного применения теплоносителей с соответствующими технологическими и теплотехническими режимами: предварительным подогревом скрапа в конвертере с использованием верхней и донных фурм в качестве горелок для стехиометрически расчетного сжигания углеводородов, дожиганием конвертерного газа верхним и боковым кислородным дутьем, введением в ванну твердых (кусковых или порошкообразных) углеродосодержащих материалов угля или кокса. Это подтверждают результаты проведенных ЦНИИчерметом исследований конвертерной плавки с повышенным расходом лома в шихте: до 3035 %, 4550 % и даже 100 %, то есть на твердой шихте без применения жидкого чугуна (рис.1).
Технология конвертерной плавки на твердой шихте без применения жидкого чугуна предусматривает выплавку качественной стали при использовании шихты, состоящей, в зависимости от конкретных условий, из металлического лома и литникового скрапа, чушкового чугуна, а также других железосодержащих материалов (металлизованных окатышей, губчатого железа и др.). В качестве теплоносителей предусматривается использование недефицитного кускового и пылевидного угольного топлива, а также вторичных углеродистых материалов, содержащих алюминий, кремний, марганец.
Возможность реконструкции энергетического оборудования конвертеров для снабжения их газообразным топливом и использования продувки по специальному режиму обеспечивает более эффективное применение предлагаемой технологии. Она является комплексной и включает ряд довольно сложных операций по регулированию шлакообразования, режимов присадки лома и кускового угля (или других топливных материалов), режимов продувки и дожигания СО и СО2 в отходящих газах, раскисления и легирования металла и т.д. Кроме того, требуется внесение определенных изменений в конструкцию фурм и сопел.
Экологическая оценка технологии конвертерной плавки с повышенным расходом лома показала, что величина запыленности отходящих газов составляет 3550 г/м3. При этом химический состав пыли и состав газовой фазы практически не отличаются от плавки по обычной технологии. Однако практика показала, что в целом продолжительность цикла плавки, а также производительность конвертеров в сравнении с обычной технологией снижается на 35 %. Кроме того, не удается полностью исключить загрязнение выплавляемой стали цветными металлами из лома.
В производстве электростали тенденция повышения доли чугуна в шихте обусловлена, во-первых, требованием снижения концентрации цветных металлов (Cr, Ni, Cu, Mo, Sn и др.) в металле, во-вторых, стремлением обеспечить экономию электроэнергии по сравнению с другими «чистыми» железосодержащими материалами, такими, как металлизованные окатыши, брикетированное железо или его карбид. При заданной мощности трансформатора снижение расхода электроэнергии одновременно означает сокращение времени подачи мощности в печь и интервала между выпусками металла, что можно использовать для наращивания производительности и дальнейшей экономии затрат (расход электродов, огнеупорных материалов и др.).
Процесс в дуговых электропечах на постоянном токе с использованием чугуна (рис. 2) позволяет снизить расход электроэнергии в одноэлектродной электропечи и по сравнению с электропечами на переменном токе оптимально использовать длину электрической дуги за счет экстенсивного образования пенистого шлака (длина электрической дуги переменного тока 400500 мм, постоянного 8001000 мм).
На практике обычно принят вариант с оптимальным соотношение лома и чугуна в пропорции 50 % + 50 % , что обеспечивает расход электроэнергии в 180 кВт.ч/т при степени дожигания 70 % и термическом кпд 80 %.
Мировая практика показывает, что в электросталеплавильном производстве для получения высококачественных марок стали применение чугуна имеет большие преимущества по сравнению с использованием других чистых загружаемых материалов, таких, как губчатое железо. Например, в результате комплексных исследований известной фирмы Iscor в печи объемом 155 т в процессе электродугового переплава шихты различного состава, в том числе с повышенным содержанием жидкого чугуна (3050 %) с применением кислорода при поддержании времени подачи мощности в печь в 45 минут удалось получить низкие концентрации фосфора и азота в металле на уровне лучших результатов, получаемых для кислородно-конвертерной стали. При этом, однако, наблюдались проблемы в процессе десульфурации, поэтому для плавки должен быть использован чугун, подвергнутый предварительной очистке от серы.
Таким образом, ни один из существующих промышленных агрегатов не решает поставленной задачи массового, экономически эффективного использования лома в сталеплавильном производстве. Это приводит к необходимости создания технологического сталеплавильного комплекса, сочетающего преимущества конвертерного производства чистых сталей с энергетическими и экологическими достоинствами электросталеплавильных процессов плазменного и дугового разряда постоянного тока. При этом в условиях возрастающих экологических требований необходимо использовать только химически и экологически чистые дополнительные теплоносители. Например, на основе теоретических и лабораторных разработок ЦНИИчерметом предложено применение низкотемпературной восстановительной плазмы в качестве дополнительного химически и экологически чистого энергоносителя в конвертерной плавке. В настоящее время ведутся работы по промышленной реализации этой технологии.
Использование низкотемпературной плазмы в кислородных конвертерах позволяет расширить сортамент выплавляемой стали и лигатур, улучшить энергетические возможности плавки, добиться легирования металла любыми необходимыми количествами добавок, получить особонизкоуглеродистые стали, не содержащие фосфора, серы и других примесей, сократить расход ферросплавов и легирующих, существенно увеличить производительность сталеплавильных цехов и улучшить экологическую обстановку.
В мировой металлургии также проявляется интерес к созданию агрегатов и технологий, совмещающих преимущества кислородного конвертера и дуговой печи постоянного тока. Фирмой Коncast Standart (Швейцария) создан Arcon-процесс, сочетающий комбинацию конвертера с верхней кислородной продувкой и одноэлектродной дуговой печи постоянного тока. Arcon-процесс обеспечивает исключительно широкие возможности использования шихты. Он позволяет загружать как горячее, так и холодное железо прямого получения, повышать долю губчатого железа в шихте в любой форме до 55 % и даже до 100 %, использовать другие железосодержащие материалы и, наконец, самое главное: металлошихта может на 100 % состоять из лома.
По сравнению с обычной дуговой печью комбинация конвертера и дуговой печи в одном Arcon-агрегате дает следующие преимущества:
широкий выбор металлошихты (жидкий и твердый чугун, металлизованные брикеты или окатыши, лом);
высокая производительность агрегата;
низкий расход электроэнергии за счет использования химической энергии окисления примесей металлошихты;
меньшая потребная электрическая мощность;
меньший удельный расход электродов;
меньшее влияние на токоведущие сети, возможность работы при маломощных электросетях и, соответственно, меньшие затраты на электрооборудование.
Применительно к российским условиям ЦНИИчерметом разработана комбинированная технология, которая заключается в выплавке железоуглеродистого расплава (жидкого синтетического чугуна ЖСЧ) из лома в дуговой печи постоянного тока (ДППТ) с последующей переработкой его в кислородном конвертере. В таблицах 1 и 2 приводится оценка энергетических затрат при выплавке стали по предлагаемому варианту в сравнении с классической схемой доменная печьконвертер и выплавкой стали на ломе в ДППТ. Среди технологических преимуществ предлагаемой схемы выплавки стали по сравнению с использованием твердого лома можно выделить:
возможность свободно варьировать соотношением доменного чугуна и лома в широких пределах до 100 % включительно (то есть ЖСЧ плюс общепринятая доля твердого лома);
возможность в процессе выплавки ЖСЧ непосредственно в ДППТ осуществлять его глубокую десульфурацию до тех же содержаний серы, что и при десульфурации доменного чугуна;
возможность использовать в качестве науглероживателя энергетических углей;
возможность подачи ЖСЧ в конвертер при строго заданной температуре в диапазоне 12501600оС и точно известным содержанием примесей цветных металлов, серы и фосфора;
при снижении спроса на сталь возможность перевода ДППТ на производство чистого по сере товарного чугуна, паспортной шихтовой заготовки, утилизации различных отходов.
Кроме того, удается обеспечить содержание азота в стали на уровне обычной конвертерной плавки, то есть вдвое ниже, чем в электростали.
Модуль ДППТ-конвертер может быть эффективно использован как на заводах с полным циклом, так и на предприятиях, не имеющих доменного производства (например, на мини-заводах). Уровень разработок в настоящее время достаточен для подготовки проектной документации.
По сравнению с выплавкой стали в ДППТ, при ее производстве по схеме ДППТконвертер расход электроэнергии непосредственно в электропечи ниже на 100 кВт . ч/т, главным образом, за счет более низкой температуры выпуска чугуна (14500С и 16500С, соответственно). При этом общие энергозатраты почти в 2,6 раза ниже, чем по схеме доменная печьконвертер и несколько ниже, чем при выплавке стали из лома в ДППТ.
Капитальные затраты на создание модуля ДППТ (то есть собственно печи в полном комплекте с необходимым непосредственно для ее эксплуатации оборудованием) на 1 т годового производства стали примерно в 4 раза ниже, чем в типовом электросталеплавильном цехе и в 1214 раз, чем по традиционной схеме доменная печьконвертер.
В качестве агрегата для выплавки ЖСЧ, по нашему мнению, следует выбрать сверхмощную двухкорпусную дуговую печь постоянного тока с подогревателями лома. Современная ДППТ такого типа емкостью 160 т обеспечивает периодические выпуски 130 т жидкой стали с интервалом в пределах 345 мин. С учетом того, что периодичность выпуска ЖСЧ будет выше (то есть цикл плавки короче), такая печь вполне может работать синхронно с конвертером, обеспечивая для конвертера емкостью 160 т возможность работы с использованием 100 % лома (130 т ЖСЧ + 3040 т твердого лома) и 60 % лома для конвертера емкостью 350 т.
Специфические конструктивные и технологические особенности конвертера позволяют обеспечить по сравнению с традиционными АКОС (печьковш) для проведения рафинировочных операций ряд преимуществ, а именно: уменьшить тепловые потери процесса нагрева и рафинирования металла благодаря более мощной футеровке, исключить на данном этапе тепловые потери, связанные с выпуском и аккумуляцией тепла футеровкой АКОС, обеспечить благодаря гораздо большему свободному объему конвертера как минимум выше на порядок интенсивность продувки ванны аргоном и соответственно интенсивность барботажа ванны, скорость массо- и теплообмена, скорость рафинирования и растворения легирующих и раскислителей. Помимо этого, использование в конвертере в разливочный период в качестве нагревателя плазмотрона постоянного тока с полым катодом позволяет: подавать через плазмотрон в струе плазмообразующего газа активные газовые окислительно-восстановительные реагенты, азот для микролегирования, порошкообразные материалы для раскисления, десульфурации, микролегирования и модифицирования в высокотемпературную и кинетически наиболее эффективную зону поверхности ванны, то есть в зону анодного пятна. Все эти факторы позволяют резко сократить период рафинирования по сравнению с АКОС. Организация нагрева металла разрядом постоянного тока облегчается тем, что это стационарный агрегат, неперемещаемый в пределах цеха, как ковш АКОС. Изготовление нагревателя вопрос технически решаемый, как и размещение анодного подового электрода. Использование конвертера взамен АКОС не требует дополнительных площадей и уменьшает капитальные затраты по сравнению с установкой АКОС на 3050 %.
Однако использование конвертера в роли АКОС требует решения ряда сопутствующих проблем. Из них к основным относятся: увеличение длительности цикла конвертерной плавки в зависимости от выплавляемого сортамента ориентировочно на 1530 мин. (в АКОС при обработке углеродистых и низколегированных сталей цикл рафинирования длится от 45 до 90 мин.), обязательное и полное удаление окислительного шлака во избежании рефосфорации. Кроме того, при встраивании предложенной технологической схемы в действующий цех необходимо согласовать работу конвертера и МНЛЗ, так как АКОС, выполняющий роль своеобразного демпфера, в данном случае отсутствует. Требуется также обеспечить на выпуске защиту струи металла от контакта с атмосферой, так как полностью раскисленный металл будет гораздо интенсивнее поглощать азот.
В принципе перечисленные технологические, организационные и технические проблемы, хотя и довольно сложны, но решаемы. В первую очередь, необходимо уточнить для конкретных условий цеха (прежде всего исходя из сортамента выплавляемых сталей), насколько в действительности будет удлиняться плавка и допустимо ли соответствующее снижение производительности конвертера.
Таким образом, экономически обоснованный комбинированный процесс существенно расширяет возможности традиционных агрегатов и открывает новые перспективы для эффективной переработки вторичного металлургического сырья.
|
|
|
|
|
текущий номер

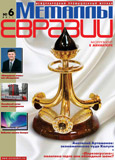
предыдущий номер

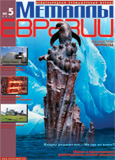
|
|