Валерий Васенев, Валерий Шариков
ОАО «Уралгипромез»
Анатолий Киричков
ОАО «НТМК»
Рельсобалочный цех НТМК находится в эксплуатации более 50 лет. Производство рельсов здесь ведется по устаревшей технологии:
рельсы прокатываются в клетях трио, не обеспечивающих геометрические параметры по сечению;
объемная закалка рельсов в масле не обеспечивает дифференцированную твердость рельсов по сечению, загрязняет атмосферу цеха и комбината продуктами термического разложения минерального масла, требует значительного расхода топлива и минерального масла. Закалка рельсов в масляной ванне не позволяет производить длинномерные рельсы, и в настоящее время цех выпускает рельсы с максимальной длиной 25 м.
Для производства рельсов, отвечающих современным требованиям, при реконструкции рельсобалочного цеха должны быть решены следующие задачи:
улучшение геометрии рельсов по сечению;
организация закалки рельсов по новой технологии, свободной от недостатков существующей и обеспечивающей производство длинномерных рельсов.
По заданию НТМК в 20012002 годах Уралгипромез выполнил предпроектную проработку коренной реконструкции рельсобалочного цеха комбината. Она показала, что для реализации указанных задач необходимо осуществить следующие мероприятия. Для улучшения геометрии рельсов по сечению их прокатка должна вестись в новых клетях более жесткой конструкции, чем у двух существующих клетей трио 800. В качестве новых возможна установка прокатных клетей дуо или клетей с универсальными калибрами.
По обоим вариантам рельсы производятся с необходимым допусками по сечению, однако их прокатка в универсальных клетях обеспечивает прямое обжатие головки по высоте рельса, вследствие чего металл получает плотную и мелкозернистую структуру. Это особенно важно для рельсов, прокатываемых из литой заготовки.
В качестве новой технологии термической обработки рельсов принята закалка рельсов водовоздушной смесью с использованием тепла прокатного нагрева. Оборудование нового термоотделения размещается за центральным холодильником. В отделении устанавливается одна закалочная линия, в которой водовоздушной смесью обрабатывается одна нитка рельсов. Рельсовый раскат длиной 51,2 м после клеймения кантуется на подошву и поступает на закалку.
Температура рельсового раската после прокатки в чистовой клети составляет 900 950 oC. Перед входом в закалочное устройство раскат проходит через индуктор, в котором его температура выравнивается.
Охлаждение рельсов производится при прохождении через секции устройства плоскими потоками охладителя, подаваемого из форсунок с дифференцированным расходом по элементам рельсов. Разбивка устройства по длине на несколько секций дает оптимальную траекторию охлаждения в различных температурных интервалах, позволяет получить оптимальную структуру по сечению головки рельса и обеспечивает сжимающее напряжение в головке и подошве рельса после охлаждения.
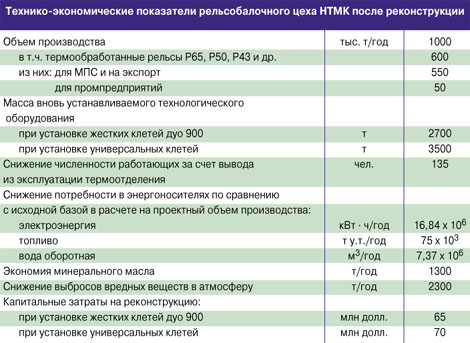
Устройство работает в проходном режиме (рельс при охлаждении проходит через закалочное устройство). Скорость транспортировки рельсов через устройство составляет 1 м/с. Температура в момент окончания охлаждения составляет для головки и подошвы 500 oC, для шейки рельса не регламентируется.
Длина закалочного устройства составляет 70 м. Расход воды на закалку рельсов 430 м3/ч, сжатого воздуха 50 тыс. нм3/ч.
Вода на закалку рельсов направляется из чистого оборотного цикла существующего термоотделения. Для ее очистки от окалины предусмотрено строительство насосно-фильтровальной станции. Для снабжения закалочного устройства сжатым воздухом предусматривается сооружение воздуходувной станции.
Установленный за закалочным устройством холодильник обеспечивает самоотпуск рельсов. Далее будет размещено следующее оборудование:
две роликоправильные машины (горизонтальная и вертикальная);
приборы контроля качества рельсов;
два отрезных станка;
правильный пресс;
два инспекторских стеллажа.
Горизонтальная девятироликовая правильная машина конструкции ОАО «Уралмаш» обеспечивает «безмоментный» способ правки, что гарантирует прямолинейность рельсов в соответствии с требованиями стандарта и помогает достичь следующего эффекта:
снизить усилия правки в 1,5 2 раза;
улучшить эпюру и существенно снизить уровень остаточных напряжений в рельсах;
уменьшить искажения поперечного профиля рельса;
повысить стабильность процесса правки.
Для обеспечения гарантии качества рельсов предусматривается установка современных приборов контроля наружных и внутренних дефектов и прямолинейности рельсов. Результаты контроля поступают в компьютер.
Далее на отрезных станках у обрабатываемой полосы удаляются невыправленные концы. Длина отрезаемых концов рельсов 600 мм. Рельсы длиной 50 м поступают на инспекторские стеллажи, где производится визуальный осмотр их поверхности и маркировка. При необходимости на гидравлическом прессе производится доправка отдельных рельсов, невыправленных на роликоправильных машинах.
Готовые рельсы будут приниматься инспекцией МПС и затем отгружаться потребителю. На каждый рельс создается паспорт, в котором указываются результаты контроля. Паспортные данные хранятся в центральном компьютере цеха столько времени, сколько это необходимо. Технико-экономические показатели работы рельсобалочного цеха после реконструкции приведены в таблице.
Рельсы, производимые в рельсобалочном цехе после его реконструкции, будут отвечать требованиям высшей категории качества В (ГОСТ Р 51685 2000). Использование рельсов длиной 50 м позволит железнодорожникам в два раза сократить количество швов при укладке рельсов в путь, а значит, сэкономить время и деньги. В настоящее время прорабатывается вопрос о дальнейшем увеличении длины выпускаемых НТМК рельсов.
|